Microchip MCP19122 Manual de Usario
Microchip
No categorizado
MCP19122
Lee a continuación 📖 el manual en español para Microchip MCP19122 (18 páginas) en la categoría No categorizado. Esta guía fue útil para 5 personas y fue valorada con 4.5 estrellas en promedio por 2 usuarios
Página 1/18
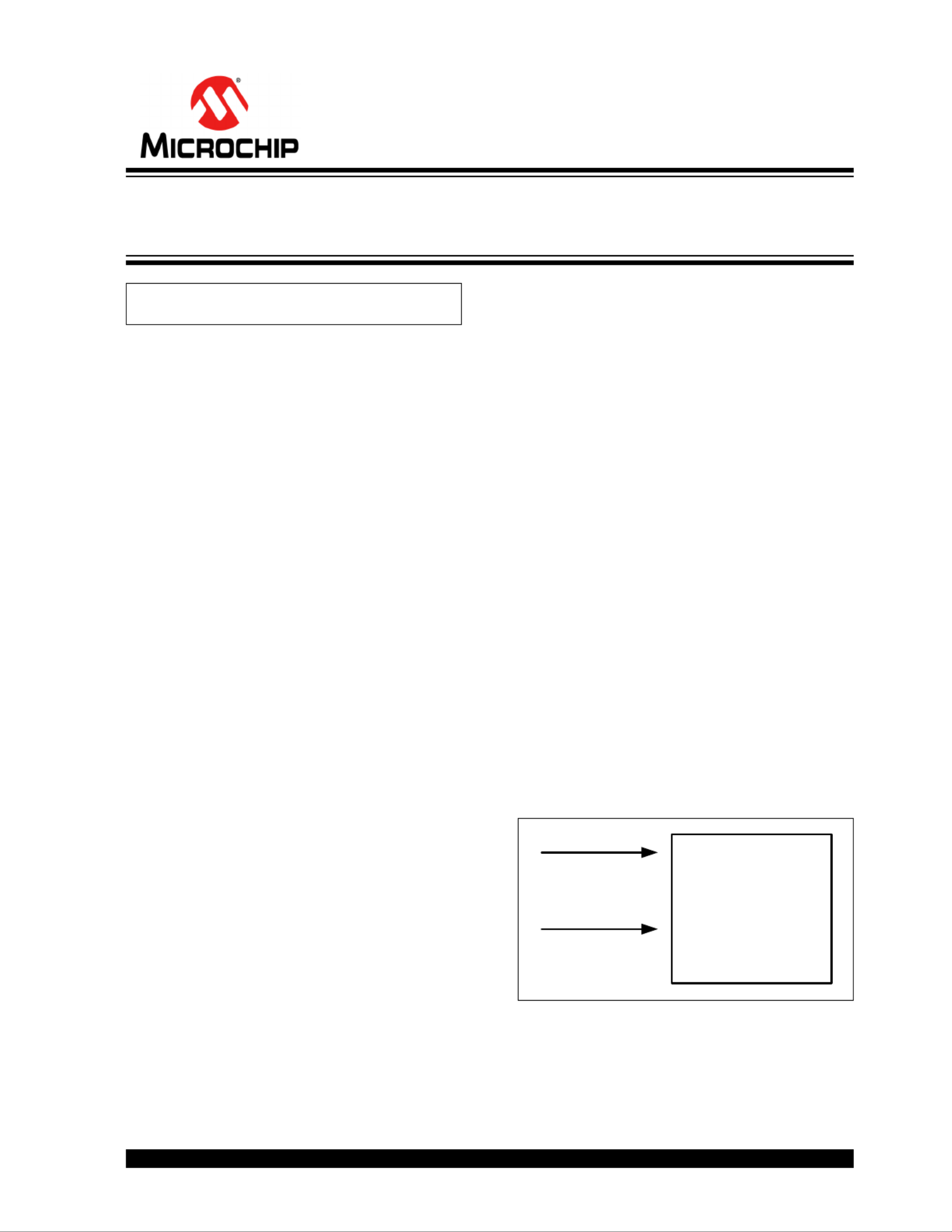
2015 Microchip Technology Inc. DS00001882A-page 1
AN1882
INTRODUCTION
In today's highly competitive and highly technological
world, analog signal measurements and regulation
accuracies are ever increasing. The MCP19114/5
Digitally Enhanced Power Analog Synchronous Low-Side
Pulse-Width Modulation Controller from Microchip
Technology Inc. is an analog controller capable of
implementing several switch-mode power supply
topologies. This analog device has the distinct advantage
of a built-in PIC® core microcontroller. The microcontroller
can be used to improve overall performance without the
penalties of additional cost or device area. This
application note provides several explanations complete
with firmware examples on how to improve ratiometric
and non-ratiometric analog signal measurements.
As a digitally enhanced power analog controller, the
MCP19114/5 has a built-in 10-bit Analog-to-Digital
Converter (ADC). When using the ADC in practice,
several factors will affect the accuracy of the
measurement. These factors include noise, offset
errors, DNL/INL errors and variations in the ADC
reference voltage. These error sources will have some
initial errors specified at room temperature (+25°C).
Also, the error due to temperature variation of these
parameters should not be overlooked. This application
note will provide a means of alleviating these errors.
Utilizing factory calibration is advantageous when
attempting to compensate for measurement errors.
However, reference voltage inaccuracies and
temperature drift will directly affect the ADC
measurement result and cannot be easily corrected.
The unique feature of an integral 8-bit PIC
microcontroller allows MCP19114/5 to implement
software solutions to help resolve these issues. To
address high-accuracy requirements of ADC
measurements and the temperature drift issues, two
methods are discussed in this application note. Both
methods require software coding and hardware
configurations. Examples are provided to better
understand these methods.
ASSUMPTIONS
This application note assumes the user:
• is familiar with MCP19114/5 digitally enhanced
analog controllers;
• has basic knowledge of Analog-to-Digital
Converters (ADC);
• has working knowledge of C programming
language.
NON-RATIOMETRIC MEASUREMENT
CORRECTION
Non-ratiometric measurements are measurements
where the signal being measured is not related to the
ADC reference. The reference voltage of MCP19114/5
ADC is AVDD. Non-ratiometric measurement correction
can be achieved by measuring a signal of known
accuracy and using this measurement to correct for
other signal measurements. This method eliminates
the need to consider variations in the ADC reference
(AVDD). The MCP19114/5 internal signal VBGR (1.23V)
is factory trimmed to within 1% and has an
overtemperature tolerance of ±2.5%. This V
BGR signal
can be read internally at the MCP19114/5 ADC through
configuration of the analog test MUX (refer to registers
ABECON and ADCON0). Non-ratiometric correction is
a mathematical approach to eliminate the ADC
reference (AVDD) tolerance errors. This method is
presented in Figure 1.
FIGURE 1: Non-ratiometric
Measurement Correction.
Author: Yiwei Xiong
Microchip Technology Inc.
MCP19114/5
ADC
VBGR
VSIGNAL
ADC Measurement Correction and Optimization
for MCP19114/5
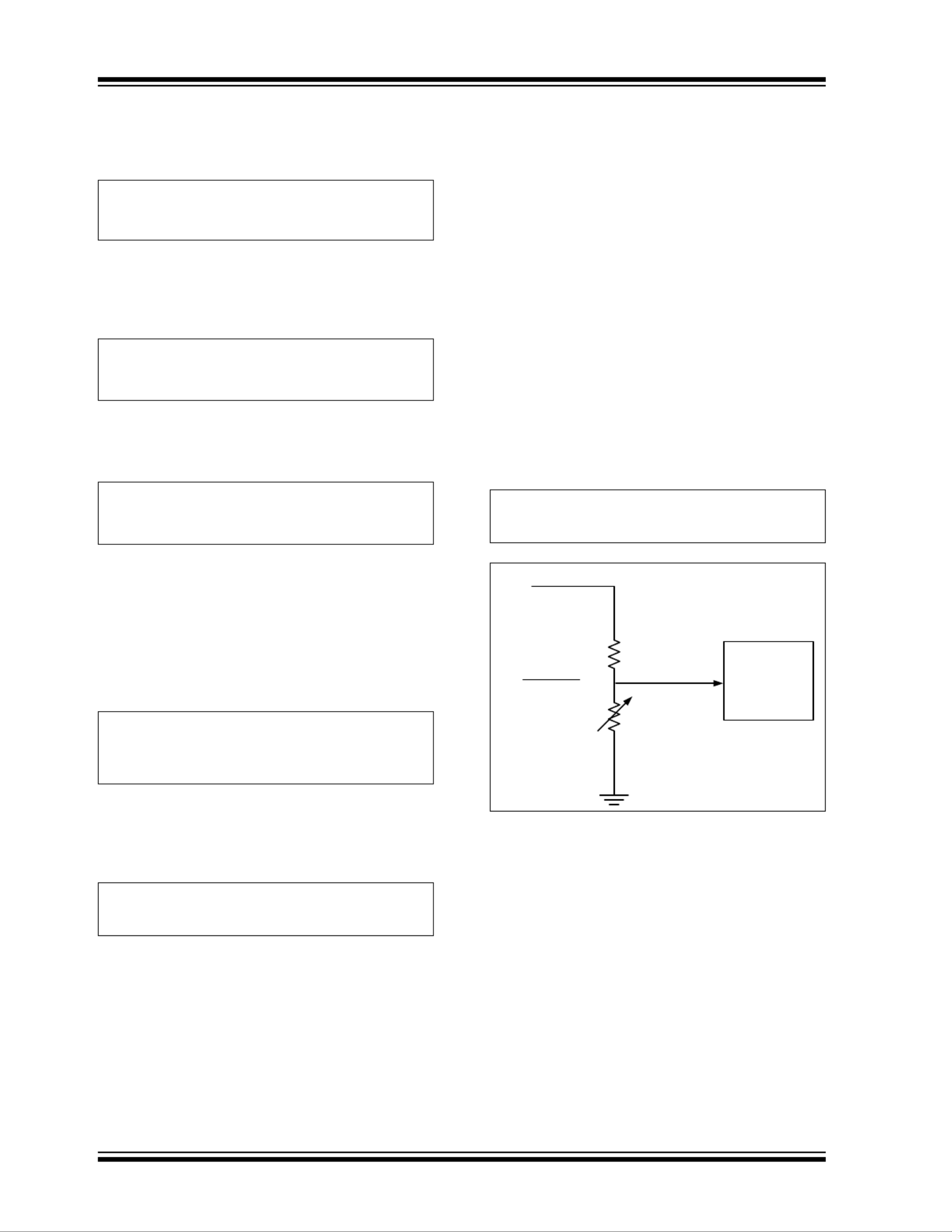
AN1882
DS00001882A-page 2 2015 Microchip Technology Inc.
First, use the ADC to measure VBGR. The measured
value V
ADC_BGR is calculated in Equation 1.
EQUATION 1:
Then, use the ADC to measure V
SIGNAL.
The measured value V
ADC_SIGNAL can be represented
as shown in Equation 2.
EQUATION 2:
Dividing Equation 1 by Equation 2 will cancel AVDD(V),
as shown in Equation 3.
EQUATION 3:
The accuracy impact of AVDD and the drift over
temperature is nullified in exchange for the more
precise VBGR signal accuracy over temperature. V
BGR
is factory trimmed to 1.23V ±1% (±2.5% over
temperature). VSIGNAL can be calculated as follows
from measured signals VADC_BGR
and VADC_SIGNAL by
rearranging Equation 3, as shown in Equation 4.
EQUATION 4:
If VSIGNAL threshold detection is desired, rearranging
Equation 4 and utilizing the known V
BGR value will pro-
vide a signal value in counts, as shown in Equation 5.
EQUATION 5:
In Equation 4 and Equation 5, the reference voltage
AVDD is replaced by VBGR so the measurement accuracy
will incur the tolerance of VBGR.
RATIOMETRIC MEASUREMENT
CORRECTION
Another means to reduce measurement error is to
implement ratiometric measurements. Typically, a
ratiometric ADC measurement is accomplished by
utilizing the same voltage source to excite the target
circuit as is used for the ADC reference. If a signal level
is beyond the ADC maximum measurement range, a
resistor divider is applied to lower the input signal with
a K-factor. The measured signal is proportional to the
reference voltage, thus, the accuracy of the
measurement depends on the sensor resistors instead
of the reference voltage. In the case of the
MCP19114/5, the ADC reference is powered from
AVDD (4V) and not the VDD (5V) regulator. The VDD
(5V) source is available externally to power-up target
circuits. To assist users desiring to make ratiometric
ADC measurements with the MCP19114/5, a factory-
stored ADC measurement value of VDD is available.
EQUATION 6:
FIGURE 2: Ratiometric Measurement
Correction.
VADC_BGR(counts)
VBGR V
AVDD V
------------------------- 1024
=
VADC_SIGNAL(counts)
VSIGNAL V
AVDD V
---------------------------------- 1024
=
VADC_BGR counts
VADC_SIGNAL counts
--------------------------------------------------------------
VBGR V
VSIGNAL V
----------------------------------=
VSIGNAL V VBGR V
VADC_SIGNAL counts
VADC_BGR counts
--------------------------------------------------------------=
VADC_SIGNAL counts VADC_BGR counts
VSIGNAL V
V
BGR V
-----------------------------------=
KR2
R1 R2+
-------------------------=
R1
R2
K =
VDD
VX = (VDD × K ) MCP19114/5
ADC
R2
R1 + R2
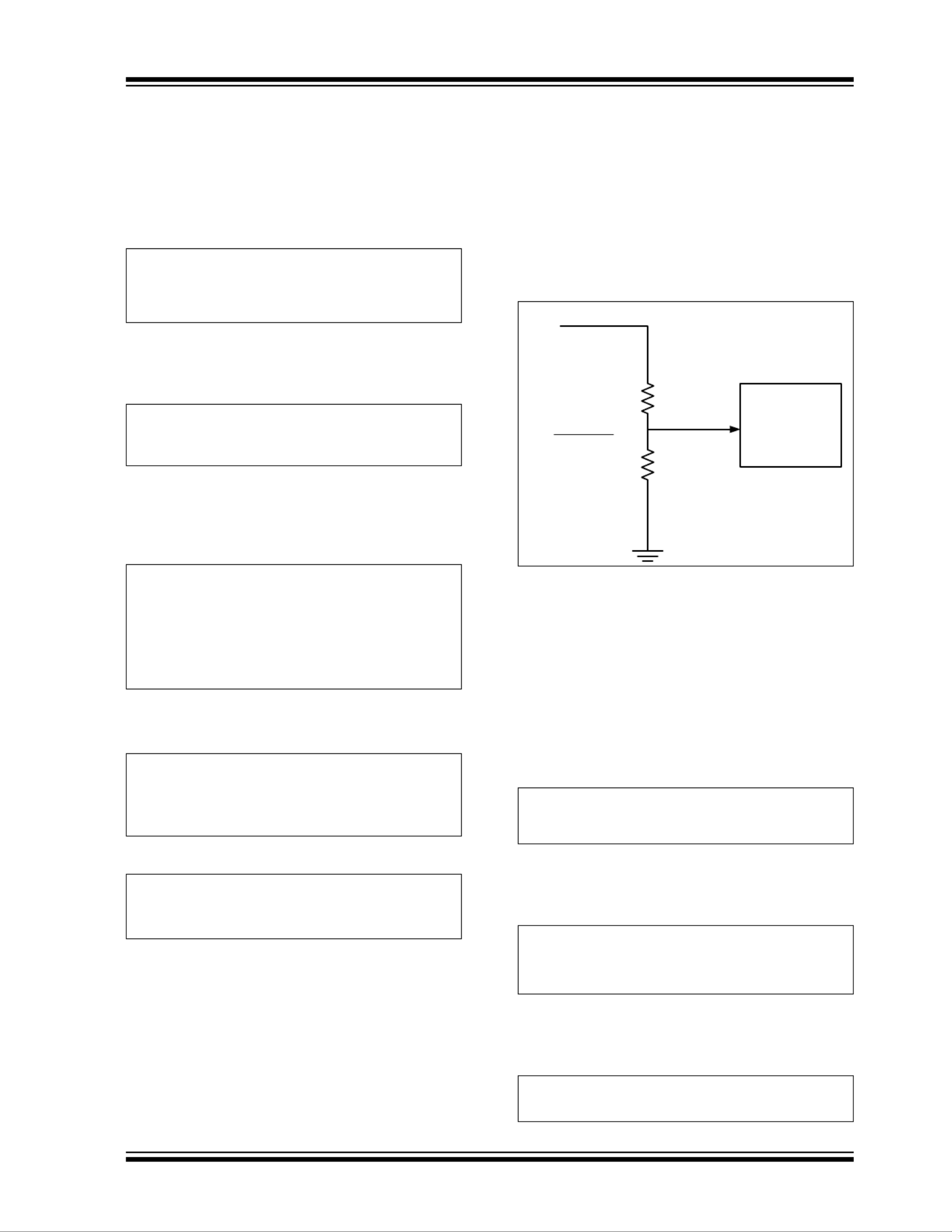
2015 Microchip Technology Inc. DS00001882A-page 3
AN1882
Calibration Word 11 stores the internal ADC reading (in
counts) of VDD/2 or half VDD (HFVDD).This is a factory-
stored value at +25°C. This value can be used to cali-
brate ratiometric ADC measurements powered from
VDD. VDD and AVDD temperature drift track to within
1.1% over temperature.
EQUATION 7:
At x°C, the ADC measurement of signal Vx°C is shown
in Equation 8.
EQUATION 8:
VDD and AVDD voltage drift will track respectively
together over temperature. Assume at temperature
x°C, VDD and AVDD drift tracks to y%.
EQUATION 9:
Divide Equation 7 by Equation 9:
EQUATION 10:
EQUATION 11:
Once KX°C is known, the R2 value can be calculated
from Equation 6. The reference voltage AV
DD is elimi-
nated from the calculation. Since the tracking tolerance
is neglected during calculation, a tracking error will be
expected in the result. See “V
DD vs. AVDD Temperature
Drift Tracking” figure in Section 2.0 Typical Perfor-
mance Curves of the MCP19114/5 Data Sheet
(DS20005281).
VOLTAGE THRESHOLD LEVEL
CHECKING USING
NON-RATIOMETRIC MEASUREMENT
Systems requiring detection of several operation points
or thresholds can implement a comparison table. Using
Equation 5, the VADC_SIGNAL (counts) can be com-
pared to the predetermined table values to perform
system operation decisions. The example shown in
Figure 3 describes the technique.
FIGURE 3: Voltage Threshold Level
Checking Using Non-ratiometric Measurement.
In Figure 3, assume a system wants to detect three
operating thresholds of input voltage V
IN:
• VIN op1 = 8V (low)
• VIN op2 = 12V (normal)
• VIN op3 = 18V (high)
Calculate the divider K based on the hardware config-
uration. In Example 1, the divider K is set to 0.14977.
EXAMPLE 1:
Ratio Reference (R) can be defined as shown in
Equation 12
EQUATION 12:
The relationship between VSIGNAL and VIN is shown in
Equation 13.
EQUATION 13:
HFVDD counts
VDD25
C
1
2
---
AVDD25
C
----------------------------------- 1024
=
Vx
Ccounts
VDDx
CKx
C
AVDDx
C
------------------------------------------- 1024
=
Vx
Ccounts
VDD25
C1 y%+
Kx
C
AVDD25
C1 y%+
--------------------------------------------------------------------------- 1024
=
VDD25
CKx
C
AVDD25
C
---------------------------------------------- 1024
=
HFVDD counts
Vx
Ccounts
--------------------------------------------
1
2
---
Kx
C
--------------=
Kx
C
Vx
Ccounts
HFVDD counts
-------------------------------------------- 1
2
---
=
R1
R2
K =
VIN
(VIN × K ) MCP19114/5
ADC
R2
R1 + R2
KR2
R1 R2+
------------------------- 0.14977==
R
VSIGNAL V
VBGR
----------------------------------=
VSIGNAL V VIN V K
=
Especificaciones del producto
Marca: | Microchip |
Categoría: | No categorizado |
Modelo: | MCP19122 |
Color del producto: | Meerkleurig |
Fácil de limpiar: | Ja |
Edad recomendada (mín.): | 1.5 maand(en) |
País de origen: | Engeland |
Número de botellas incluidas: | 1 |
Capacidad-de-la-botella: | 340 ml |
¿Necesitas ayuda?
Si necesitas ayuda con Microchip MCP19122 haz una pregunta a continuación y otros usuarios te responderán
No categorizado Microchip Manuales

27 Octubre 2024

27 Octubre 2024

27 Octubre 2024

27 Octubre 2024

27 Octubre 2024

27 Octubre 2024

27 Octubre 2024

27 Octubre 2024

27 Octubre 2024

27 Octubre 2024
No categorizado Manuales
- No categorizado Candy
- No categorizado Sony
- No categorizado Electrolux
- No categorizado Samsung
- No categorizado Xiaomi
- No categorizado Casio
- No categorizado ATAG
- No categorizado LG
- No categorizado Bosch
- No categorizado AEG
- No categorizado IKEA
- No categorizado Huawei
- No categorizado Braun
- No categorizado HP
- No categorizado Philips
- No categorizado Panasonic
- No categorizado Bauknecht
- No categorizado BEKO
- No categorizado Delonghi
- No categorizado Daewoo
- No categorizado DeWalt
- No categorizado Epson
- No categorizado Etna
- No categorizado Ford
- No categorizado Fysic
- No categorizado Garmin
- No categorizado Grundig
- No categorizado Honeywell
- No categorizado Indesit
- No categorizado Inventum
- No categorizado JVC
- No categorizado JBL
- No categorizado Junkers
- No categorizado Kenwood
- No categorizado Krups
- No categorizado Karcher
- No categorizado Liebherr
- No categorizado Miele
- No categorizado Motorola
- No categorizado Medion
- No categorizado Nikon
- No categorizado Olympus
- No categorizado Onkyo
- No categorizado Pioneer
- No categorizado Quigg
- No categorizado Ravensburger
- No categorizado Siemens
- No categorizado Toshiba
- No categorizado Unold
- No categorizado VTech
- No categorizado Whirlpool
- No categorizado WOLF-Garten
- No categorizado Wiko
- No categorizado Yamaha
- No categorizado Yealink
- No categorizado Zanussi
- No categorizado Tefal
- No categorizado Vaillant
- No categorizado Canon
- No categorizado Lego
- No categorizado Volvo
- No categorizado A.O. Smith
- No categorizado Ade
- No categorizado Adidas
- No categorizado Adler
- No categorizado Abus
- No categorizado Ag Neovo
- No categorizado Aduro
- No categorizado Acer
- No categorizado ACCU-CHEK
- No categorizado Aiwa
- No categorizado Al-ko
- No categorizado Alcatel
- No categorizado Allnet
- No categorizado Alpina
- No categorizado Ambiano
- No categorizado Albrecht
- No categorizado Amica
- No categorizado Alecto
- No categorizado Airlux
- No categorizado Aligator
- No categorizado Akg
- No categorizado AOC
- No categorizado Akai
- No categorizado Alphatronics
- No categorizado Afk
- No categorizado Apc
- No categorizado Allied Telesis
- No categorizado Alienware
- No categorizado Alpine
- No categorizado Amana
- No categorizado Aluratek
- No categorizado ABC Design
- No categorizado Amfra
- No categorizado Amazfit
- No categorizado Ansmann
- No categorizado Alesis
- No categorizado Apple
- No categorizado Advance Acoustic
- No categorizado Alcon
- No categorizado Amazon
- No categorizado Airlive
- No categorizado Anker
- No categorizado A4tech
- No categorizado Ampeg
- No categorizado Amplicom
- No categorizado Amprobe
- No categorizado Archos
- No categorizado Argon
- No categorizado Ariete
- No categorizado Arendo
- No categorizado Arcelik
- No categorizado American Audio
- No categorizado Aprilia
- No categorizado Aquapur
- No categorizado Acti
- No categorizado Akasa
- No categorizado Amiko
- No categorizado Aeris
- No categorizado Ascom
- No categorizado Arturia
- No categorizado Alpen Kreuzer
- No categorizado Asko
- No categorizado ACME
- No categorizado Alto
- No categorizado Reflecta
- No categorizado Silverline
- No categorizado Argus
- No categorizado Joie
- No categorizado Suunto
- No categorizado ATN
- No categorizado Bartscher
- No categorizado Prestigio
- No categorizado Edimax
- No categorizado Intermatic
- No categorizado Strong
- No categorizado Toolland
- No categorizado Icy Box
- No categorizado Adventuridge
- No categorizado Brennenstuhl
- No categorizado Ferm
- No categorizado OneConcept
- No categorizado Hirschmann
- No categorizado Vileda
- No categorizado Absima
- No categorizado Google
- No categorizado Hikvision
- No categorizado Audison
- No categorizado Arris
- No categorizado Workzone
- No categorizado Sabo
- No categorizado Eurom
- No categorizado Shark
- No categorizado GE
- No categorizado Orbegozo
- No categorizado Salton
- No categorizado Proteca
- No categorizado Princess
- No categorizado Generac
- No categorizado Topmove
- No categorizado Subaru
- No categorizado BenQ
- No categorizado Lexibook
- No categorizado Brother
- No categorizado Ozito
- No categorizado Gude
- No categorizado Sharp
- No categorizado Fisher And Paykel
- No categorizado Bertazzoni
- No categorizado Loewe
- No categorizado Leica
- No categorizado Klarstein
- No categorizado Fagor
- No categorizado Omega
- No categorizado Severin
- No categorizado Smeg
- No categorizado Telefunken
- No categorizado Gorenje
- No categorizado Neff
- No categorizado Silvercrest
- No categorizado Jysk
- No categorizado Toorx
- No categorizado Body Solid
- No categorizado Makita
- No categorizado Draper
- No categorizado Tryton
- No categorizado Hitachi
- No categorizado Spektrum
- No categorizado Nedis
- No categorizado Thomson
- No categorizado Arthur Martin
- No categorizado Oceanic
- No categorizado Korona
- No categorizado Gembird
- No categorizado Hoover
- No categorizado Saturn
- No categorizado Black And Decker
- No categorizado Bestway
- No categorizado Breville
- No categorizado Tiger
- No categorizado KitchenAid
- No categorizado Innoliving
- No categorizado Tristar
- No categorizado Domo
- No categorizado Teka
- No categorizado Trisa
- No categorizado Yale
- No categorizado Progress
- No categorizado Lenco
- No categorizado GoPro
- No categorizado Cata
- No categorizado Pyle
- No categorizado Gaggenau
- No categorizado Vonroc
- No categorizado Hotpoint-Ariston
- No categorizado Meradiso
- No categorizado Calor
- No categorizado Remington
- No categorizado Rowenta
- No categorizado Waring Commercial
- No categorizado Taylor
- No categorizado Kernau
- No categorizado Maytag
- No categorizado Miomare
- No categorizado Maxi-Cosi
- No categorizado Livoo
- No categorizado BH Fitness
- No categorizado OBH Nordica
- No categorizado Stanley
- No categorizado Manta
- No categorizado Tevion
- No categorizado Crivit
- No categorizado Asus
- No categorizado GPO
- No categorizado Thermador
- No categorizado Lucide
- No categorizado Parisot
- No categorizado Caliber
- No categorizado SereneLife
- No categorizado Beurer
- No categorizado Smoby
- No categorizado Skil
- No categorizado Hisense
- No categorizado Hyundai
- No categorizado Hanseatic
- No categorizado Vox
- No categorizado Cylinda
- No categorizado Yato
- No categorizado Dyson
- No categorizado Bestron
- No categorizado Bellini
- No categorizado BaByliss
- No categorizado Eminent
- No categorizado Pressalit
- No categorizado Hilti
- No categorizado SilverStone
- No categorizado Avanti
- No categorizado Oster
- No categorizado Kichler
- No categorizado VAX
- No categorizado Trekstor
- No categorizado Renkforce
- No categorizado Westinghouse
- No categorizado Cherry
- No categorizado ECG
- No categorizado Moulinex
- No categorizado Izzy
- No categorizado Kodak
- No categorizado Bushnell
- No categorizado Pelgrim
- No categorizado Blomberg
- No categorizado Ryobi
- No categorizado Bush
- No categorizado Jata
- No categorizado Rapoo
- No categorizado LC-Power
- No categorizado Sharkoon
- No categorizado Melissa
- No categorizado Magic Chef
- No categorizado Florabest
- No categorizado VirtuFit
- No categorizado Swan
- No categorizado Emerio
- No categorizado RCA
- No categorizado Scarlett
- No categorizado Clatronic
- No categorizado Fritel
- No categorizado Taurus
- No categorizado Ordex
- No categorizado Itho
- No categorizado Russell Hobbs
- No categorizado Elica
- No categorizado Constructa
- No categorizado Targus
- No categorizado Summit
- No categorizado Hotpoint
- No categorizado Q-CONNECT
- No categorizado Lowrance
- No categorizado Chicco
- No categorizado Sencor
- No categorizado Midea
- No categorizado Lanaform
- No categorizado Conair
- No categorizado Jane
- No categorizado Landmann
- No categorizado 3M
- No categorizado Sicce
- No categorizado Overmax
- No categorizado Vivanco
- No categorizado Niceboy
- No categorizado Cuisinart
- No categorizado GPX
- No categorizado Outwell
- No categorizado Festool
- No categorizado Sitecom
- No categorizado Blaupunkt
- No categorizado Metabo
- No categorizado TP Link
- No categorizado Juki
- No categorizado Megasat
- No categorizado Britax
- No categorizado United Office
- No categorizado Logitech
- No categorizado Concept
- No categorizado Cybex
- No categorizado Gram
- No categorizado Monogram
- No categorizado Spanninga
- No categorizado Lenovo
- No categorizado Solac
- No categorizado Manhattan
- No categorizado Frigidaire
- No categorizado Jura
- No categorizado Sunbeam
- No categorizado ZOTAC
- No categorizado BeamZ
- No categorizado Parkside
- No categorizado Worx
- No categorizado Svan
- No categorizado Hard Head
- No categorizado Exibel
- No categorizado Logik
- No categorizado Medisana
- No categorizado Medela
- No categorizado NAD
- No categorizado Easy Camp
- No categorizado Danby
- No categorizado Anslut
- No categorizado Balay
- No categorizado Texas Instruments
- No categorizado Ezviz
- No categorizado Bowers And Wilkins
- No categorizado Meec Tools
- No categorizado Thermaltake
- No categorizado Energy Sistem
- No categorizado Orbit
- No categorizado Black Box
- No categorizado Audio-Technica
- No categorizado Humminbird
- No categorizado Auto Joe
- No categorizado Polaroid
- No categorizado Trust
- No categorizado Cardo
- No categorizado KEF
- No categorizado Milwaukee
- No categorizado Fortinet
- No categorizado PKM
- No categorizado Youin
- No categorizado Daikin
- No categorizado Hikoki
- No categorizado Carson
- No categorizado Telestar
- No categorizado Elro
- No categorizado Valore
- No categorizado Crunch
- No categorizado Accucold
- No categorizado Sun Joe
- No categorizado Frilec
- No categorizado Perfecta
- No categorizado EMOS
- No categorizado Doro
- No categorizado Sagem
- No categorizado Teesa
- No categorizado Extech
- No categorizado Jumbo
- No categorizado Rosieres
- No categorizado Cricut
- No categorizado Mesko
- No categorizado Hähnel
- No categorizado Ferplast
- No categorizado Melitta
- No categorizado Salora
- No categorizado Aukey
- No categorizado Profilo
- No categorizado Tunturi
- No categorizado Dremel
- No categorizado Victron Energy
- No categorizado Avaya
- No categorizado Cramer
- No categorizado Ernesto
- No categorizado KlikaanKlikuit
- No categorizado KKT Kolbe
- No categorizado Gemini
- No categorizado Easypix
- No categorizado Beper
- No categorizado Denver
- No categorizado Omron
- No categorizado Thetford
- No categorizado Ei Electronics
- No categorizado Thule
- No categorizado Berg
- No categorizado Tripp Lite
- No categorizado Simplified MFG
- No categorizado Truma
- No categorizado Optoma
- No categorizado CDA
- No categorizado Vision
- No categorizado Bissell
- No categorizado ABB
- No categorizado Genie
- No categorizado Imperial
- No categorizado Hendi
- No categorizado Suzuki
- No categorizado Mellerware
- No categorizado President
- No categorizado Intex
- No categorizado Stinger
- No categorizado Toa
- No categorizado Roland
- No categorizado Silva
- No categorizado DataVideo
- No categorizado ZTE
- No categorizado Energenie
- No categorizado Optex
- No categorizado Hazet
- No categorizado Bebe Confort
- No categorizado Heinner
- No categorizado Schneider
- No categorizado Termozeta
- No categorizado Bella
- No categorizado Axis
- No categorizado Metrix
- No categorizado Vitek
- No categorizado Palson
- No categorizado ART
- No categorizado Benning
- No categorizado Eldom
- No categorizado Valeton
- No categorizado Jocca
- No categorizado Nilox
- No categorizado Vango
- No categorizado Einhell
- No categorizado Ultimate Speed
- No categorizado Hama
- No categorizado Tiptop Audio
- No categorizado Sonos
- No categorizado Soundmaster
- No categorizado SKS
- No categorizado Hifonics
- No categorizado Fujifilm
- No categorizado Musway
- No categorizado Kensington
- No categorizado Nautilus
- No categorizado Byron
- No categorizado Maxxmee
- No categorizado Brigmton
- No categorizado Voltcraft
- No categorizado Kenmore
- No categorizado Denon
- No categorizado Sunstech
- No categorizado Bang And Olufsen
- No categorizado Vonyx
- No categorizado Gardena
- No categorizado Sennheiser
- No categorizado Philco
- No categorizado Weller
- No categorizado Theben
- No categorizado Bryton
- No categorizado Smith & Wesson
- No categorizado AVM
- No categorizado Reich
- No categorizado TCL
- No categorizado Elektrobock
- No categorizado Chamberlain
- No categorizado Gigabyte
- No categorizado Nabo
- No categorizado Guzzanti
- No categorizado Defy
- No categorizado Stiebel Eltron
- No categorizado DeLock
- No categorizado Plant Craft
- No categorizado Infiniton
- No categorizado Thorens
- No categorizado Terraillon
- No categorizado Baumr-AG
- No categorizado Bionaire
- No categorizado Maginon
- No categorizado Midland
- No categorizado Konica Minolta
- No categorizado Sylvania
- No categorizado Mitsubishi
- No categorizado Dometic
- No categorizado Lasko
- No categorizado Campomatic
- No categorizado Patton
- No categorizado Igloo
- No categorizado Aspes
- No categorizado Velleman
- No categorizado Senco
- No categorizado Hayward
- No categorizado Ninja
- No categorizado Hauck
- No categorizado Bialetti
- No categorizado Microsoft
- No categorizado Nec
- No categorizado SanDisk
- No categorizado Zoofari
- No categorizado Techly
- No categorizado Dimplex
- No categorizado DCG
- No categorizado Yard Force
- No categorizado Numatic
- No categorizado Swissvoice
- No categorizado Korg
- No categorizado Varta
- No categorizado Emerson
- No categorizado Vaude
- No categorizado Totolink
- No categorizado Eheim
- No categorizado GlobalTronics
- No categorizado Vemer
- No categorizado Smartwares
- No categorizado LD Systems
- No categorizado Sunny
- No categorizado Technisat
- No categorizado La Crosse Technology
- No categorizado Easymaxx
- No categorizado GoGEN
- No categorizado Inglesina
- No categorizado Suntec
- No categorizado BBB
- No categorizado BlueBuilt
- No categorizado Peugeot
- No categorizado Rockford Fosgate
- No categorizado Blanco
- No categorizado BDI
- No categorizado Profile
- No categorizado Marquant
- No categorizado Orima
- No categorizado Nibe
- No categorizado Damixa
- No categorizado Bogen
- No categorizado Da-Lite
- No categorizado Trebs
- No categorizado Bugaboo
- No categorizado Ferroli
- No categorizado Ednet
- No categorizado Technics
- No categorizado Luxor
- No categorizado Solis
- No categorizado Cisco
- No categorizado Bowflex
- No categorizado Husqvarna
- No categorizado AVerMedia
- No categorizado Visage
- No categorizado Koenic
- No categorizado Sena
- No categorizado Celestron
- No categorizado Falmec
- No categorizado Haier
- No categorizado American DJ
- No categorizado Master Lock
- No categorizado Krüger And Matz
- No categorizado Salus
- No categorizado Matrox
- No categorizado Seiko
- No categorizado Rangemaster
- No categorizado Maktec
- No categorizado Kubota
- No categorizado Forza
- No categorizado Gree
- No categorizado H.Koenig
- No categorizado Binatone
- No categorizado Connect IT
- No categorizado Eufy
- No categorizado Steren
- No categorizado Haeger
- No categorizado Allen & Heath
- No categorizado Perel
- No categorizado Steba
- No categorizado Engenius
- No categorizado Viking
- No categorizado Nuna
- No categorizado Iiyama
- No categorizado Tanita
- No categorizado Burg-Wachter
- No categorizado Eico
- No categorizado Kicker
- No categorizado Bose
- No categorizado Kyoritsu
- No categorizado Nero
- No categorizado Lumens
- No categorizado Thor
- No categorizado Sensiplast
- No categorizado Steinel
- No categorizado Fitbit
- No categorizado Kubo
- No categorizado Benavent
- No categorizado IFM
- No categorizado Beem
- No categorizado Pro-User
- No categorizado Air King
- No categorizado Tanaka
- No categorizado Exquisit
- No categorizado Mattel
- No categorizado Gossen
- No categorizado Elba
- No categorizado Ideal
- No categorizado Flir
- No categorizado Homedics
- No categorizado Paidi
- No categorizado Clarion
- No categorizado Somfy
- No categorizado SBS
- No categorizado KiddyGuard
- No categorizado Proline
- No categorizado Livarno
- No categorizado Barkan
- No categorizado Grohe
- No categorizado Fresh N Rebel
- No categorizado Netis
- No categorizado Sanitas
- No categorizado Coby
- No categorizado Lorelli
- No categorizado Euromaid
- No categorizado Royal Sovereign
- No categorizado HTC
- No categorizado Corberó
- No categorizado King
- No categorizado Crosley
- No categorizado Domyos
- No categorizado Ergobaby
- No categorizado New Pol
- No categorizado Zelmer
- No categorizado Mackie
- No categorizado Envivo
- No categorizado Muse
- No categorizado Petzl
- No categorizado Teufel
- No categorizado Auriol
- No categorizado Marantz
- No categorizado Fujitsu
- No categorizado True
- No categorizado Ardes
- No categorizado AJA
- No categorizado Gustavsberg
- No categorizado Mac Audio
- No categorizado Galaxy Audio
- No categorizado Be Quiet!
- No categorizado Black Diamond
- No categorizado Rega
- No categorizado ESYLUX
- No categorizado Ventus
- No categorizado Melinera
- No categorizado Nutrichef
- No categorizado Pro-Ject
- No categorizado Craftsman
- No categorizado Fisher Price
- No categorizado Technoline
- No categorizado Genius
- No categorizado Lindam
- No categorizado Metz
- No categorizado Adj
- No categorizado Kelvinator
- No categorizado Sage
- No categorizado ETA
- No categorizado Oase
- No categorizado Biltema
- No categorizado Yamato
- No categorizado Life Fitness
- No categorizado Belgacom
- No categorizado Digitus
- No categorizado Kathrein
- No categorizado Malmbergs
- No categorizado Phoenix
- No categorizado Asrock
- No categorizado Nitecore
- No categorizado Draytek
- No categorizado AV:link
- No categorizado Olympia
- No categorizado Power Craft
- No categorizado GBC
- No categorizado Belkin
- No categorizado Prenatal
- No categorizado Champion
- No categorizado Soler And Palau
- No categorizado Tvilum
- No categorizado Razer
- No categorizado Stadler Form
- No categorizado Devolo
- No categorizado Heylo
- No categorizado Mio
- No categorizado TacTic
- No categorizado Neumann
- No categorizado Geuther
- No categorizado G3
- No categorizado Zephyr
- No categorizado Peach
- No categorizado Trixie
- No categorizado Bomann
- No categorizado Pure
- No categorizado Snow Joe
- No categorizado GRE
- No categorizado Finnlo
- No categorizado DJI
- No categorizado Proficare
- No categorizado Hamilton Beach
- No categorizado Novy
- No categorizado Dymo
- No categorizado Linksys
- No categorizado Lescha
- No categorizado Capital Sports
- No categorizado Pulsar
- No categorizado RCF
- No categorizado Kuppersbusch
- No categorizado Barco
- No categorizado Buffalo
- No categorizado Continental Edison
- No categorizado Vello
- No categorizado Lamax
- No categorizado Wmf
- No categorizado Jenn-Air
- No categorizado Powerplus
- No categorizado R-Vent
- No categorizado Graef
- No categorizado Stiga
- No categorizado Audioline
- No categorizado Porter-Cable
- No categorizado Woood
- No categorizado Uniden
- No categorizado Dahua Technology
- No categorizado Klipsch
- No categorizado Audiovox
- No categorizado Carpigiani
- No categorizado Ion
- No categorizado Cotech
- No categorizado Insignia
- No categorizado Renegade
- No categorizado Davis
- No categorizado ICU
- No categorizado Rossmax
- No categorizado Nacon
- No categorizado Edesa
- No categorizado Sanus
- No categorizado Farberware
- No categorizado Ufesa
- No categorizado CasaFan
- No categorizado Viessmann
- No categorizado Milectric
- No categorizado Vicks
- No categorizado Mobicool
- No categorizado Supermicro
- No categorizado Yaesu
- No categorizado Microlife
- No categorizado Rommelsbacher
- No categorizado Walkstool
- No categorizado Rollei
- No categorizado Macally
- No categorizado Wilfa
- No categorizado GeoVision
- No categorizado Kidde
- No categorizado Apogee
- No categorizado Carrier
- No categorizado Peerless-AV
- No categorizado Netgear
- No categorizado Vogels
- No categorizado Growatt
- No categorizado Artsound
- No categorizado Nest
- No categorizado Grothe
- No categorizado LevelOne
- No categorizado Kwantum
- No categorizado Genesis
- No categorizado Pyle Pro
- No categorizado Peavey
- No categorizado BT
- No categorizado MXL
- No categorizado Testboy
- No categorizado Transcend
- No categorizado Goclever
- No categorizado Wehkamp
- No categorizado Evenflo
- No categorizado Profoon
- No categorizado Svedbergs
- No categorizado Kaiser
- No categorizado QNAP
- No categorizado Salter
- No categorizado Dual
- No categorizado Osprey
- No categorizado Trotec
- No categorizado Graco
- No categorizado Maglite
- No categorizado DIO
- No categorizado Boss
- No categorizado Ninebot
- No categorizado George Foreman
- No categorizado Cilio
- No categorizado McIntosh
- No categorizado LaCie
- No categorizado Itho-Daalderop
- No categorizado Maul
- No categorizado Sigma
- No categorizado BabyOno
- No categorizado Bixolon
- No categorizado Karibu
- No categorizado Troy-Bilt
- No categorizado Fellowes
- No categorizado Asaklitt
- No categorizado Ricoh
- No categorizado Oricom
- No categorizado Behringer
- No categorizado Laica
- No categorizado Samac
- No categorizado Brevi
- No categorizado Waterpik
- No categorizado Franke
- No categorizado Stokke
- No categorizado Sodastream
- No categorizado SMA
- No categorizado Kayser
- No categorizado AYA
- No categorizado Autotek
- No categorizado Safety 1st
- No categorizado PreSonus
- No categorizado Hive
- No categorizado Danfoss
- No categorizado Peg Perego
- No categorizado Brabantia
- No categorizado Camry
- No categorizado AS - Schwabe
- No categorizado Fissler
- No categorizado Kayoba
- No categorizado NOCO
- No categorizado Lexmark
- No categorizado Native Instruments
- No categorizado Cobra
- No categorizado MB Quart
- No categorizado Inkbird
- No categorizado NGS
- No categorizado Nodor
- No categorizado Shimano
- No categorizado Godox
- No categorizado Marshall
- No categorizado Dell
- No categorizado Electro-Voice
- No categorizado Valcom
- No categorizado Goobay
- No categorizado Hammer
- No categorizado Switel
- No categorizado Hager
- No categorizado Bresser
- No categorizado Olight
- No categorizado Liftmaster
- No categorizado Bopita
- No categorizado FireAngel
- No categorizado Challenge
- No categorizado Tascam
- No categorizado Mercusys
- No categorizado Chacon
- No categorizado Astro
- No categorizado Imetec
- No categorizado Focal
- No categorizado Salta
- No categorizado InFocus
- No categorizado Focusrite
- No categorizado Topcraft
- No categorizado Kraftwerk
- No categorizado Texas
- No categorizado Naish
- No categorizado Festo
- No categorizado Olivetti
- No categorizado Massive
- No categorizado Barska
- No categorizado Wacom
- No categorizado Auna
- No categorizado Weihrauch Sport
- No categorizado Blaze
- No categorizado Dirt Devil
- No categorizado Hombli
- No categorizado Martha Stewart
- No categorizado Reolink
- No categorizado Milan
- No categorizado Lümme
- No categorizado Jocel
- No categorizado First Alert
- No categorizado Springfree
- No categorizado Ansco
- No categorizado Crock-Pot
- No categorizado Glem Gas
- No categorizado Xblitz
- No categorizado IK Multimedia
- No categorizado Elation
- No categorizado Goodram
- No categorizado MADE
- No categorizado Noma
- No categorizado TFA
- No categorizado Spear & Jackson
- No categorizado Jabra
- No categorizado Scheppach
- No categorizado IDance
- No categorizado Habitat
- No categorizado Samson
- No categorizado Atika
- No categorizado Maxview
- No categorizado Bifinett
- No categorizado U-Line
- No categorizado Honda
- No categorizado Planet
- No categorizado Yongnuo
- No categorizado Zhiyun
- No categorizado Boso
- No categorizado Wagner
- No categorizado Gamma
- No categorizado Proctor Silex
- No categorizado Elite
- No categorizado Zodiac
- No categorizado Rupert Neve Designs
- No categorizado Carel
- No categorizado BOHLT
- No categorizado Handicare
- No categorizado ZyXEL
- No categorizado McCulloch
- No categorizado Primo
- No categorizado Rocketfish
- No categorizado Little Tikes
- No categorizado Hunter
- No categorizado Speed-Link
- No categorizado Laser
- No categorizado Creda
- No categorizado Tower
- No categorizado Comfee
- No categorizado Honor
- No categorizado Clas Ohlson
- No categorizado Baninni
- No categorizado Gastroback
- No categorizado Naxa
- No categorizado Nemef
- No categorizado TomTom
- No categorizado Viper
- No categorizado Meireles
- No categorizado Powerfix
- No categorizado RugGear
- No categorizado Sven
- No categorizado Technika
- No categorizado Saro
- No categorizado Millenium
- No categorizado Vogue
- No categorizado Grixx
- No categorizado Navitel
- No categorizado Topeak
- No categorizado Owon
- No categorizado V-Zug
- No categorizado SuperFish
- No categorizado Sauber
- No categorizado Aqua Joe
- No categorizado Shure
- No categorizado Innovaphone
- No categorizado Intel
- No categorizado Mamiya
- No categorizado MPM
- No categorizado Zuiver
- No categorizado Pentax
- No categorizado Fantec
- No categorizado Konig
- No categorizado Nextbase
- No categorizado Reloop
- No categorizado Delta
- No categorizado Valueline
- No categorizado Rotel
- No categorizado Becken
- No categorizado Trigano
- No categorizado Chandler
- No categorizado Corel
- No categorizado Hozelock
- No categorizado Sweex
- No categorizado Busch And Müller
- No categorizado Ices
- No categorizado Trevi
- No categorizado Reer
- No categorizado Vizio
- No categorizado Tesla
- No categorizado Schuberth
- No categorizado MSI
- No categorizado Rademacher
- No categorizado Char-Broil
- No categorizado RDL
- No categorizado Foscam
- No categorizado Austrian Audio
- No categorizado Vakoss
- No categorizado Silkn
- No categorizado Eberspacher
- No categorizado Kress
- No categorizado Hobby
- No categorizado Busch-Jaeger
- No categorizado Zehnder
- No categorizado Stihl
- No categorizado Laurastar
- No categorizado Bavaria
- No categorizado Mx Onda
- No categorizado Zenit
- No categorizado Orion
- No categorizado JL Audio
- No categorizado Juwel
- No categorizado Zebra
- No categorizado Wacker Neuson
- No categorizado EVE
- No categorizado Wharfedale
- No categorizado Marvel
- No categorizado Chord
- No categorizado Xterra
- No categorizado Soundcraft
- No categorizado Fredenstein
- No categorizado Viewsonic
- No categorizado Playmobil
- No categorizado Tesy
- No categorizado Napoleon
- No categorizado Nanni
- No categorizado Fuji
- No categorizado Swissonic
- No categorizado Razor
- No categorizado Schütte
- No categorizado Shindaiwa
- No categorizado Technaxx
- No categorizado D-Link
- No categorizado BRIO
- No categorizado Waeco
- No categorizado Natec
- No categorizado Fiio
- No categorizado RGV
- No categorizado Ikan
- No categorizado Elkay
- No categorizado Tamiya
- No categorizado Mestic
- No categorizado Logicom
- No categorizado Swann
- No categorizado Alfen
- No categorizado Rexel
- No categorizado Withings
- No categorizado Sound Machines
- No categorizado Tepro
- No categorizado Team
- No categorizado Lionelo
- No categorizado Petsafe
- No categorizado Sunding
- No categorizado Nelson
- No categorizado Nilfisk
- No categorizado Foppapedretti
- No categorizado TranzX
- No categorizado Chauvet
- No categorizado Flex
- No categorizado Aviom
- No categorizado Tenda
- No categorizado Cooler Master
- No categorizado UPM
- No categorizado Happy Plugs
- No categorizado BABY Born
- No categorizado Privileg
- No categorizado One For All
- No categorizado Dynacord
- No categorizado T'nB
- No categorizado ProfiCook
- No categorizado Ematic
- No categorizado Finder
- No categorizado Fluke
- No categorizado Levoit
- No categorizado QSC
- No categorizado Vivax
- No categorizado Phonak
- No categorizado Winix
- No categorizado Emporia
- No categorizado Faber
- No categorizado Hartan
- No categorizado Hasbro
- No categorizado Hamax
- No categorizado Xavax
- No categorizado Emmaljunga
- No categorizado Fantini Cosmi
- No categorizado X4-Tech
- No categorizado Traxxas
- No categorizado Tracer
- No categorizado Audac
- No categorizado Nevir
- No categorizado Eltako
- No categorizado Marmitek
- No categorizado Sekonic
- No categorizado Azden
- No categorizado Kyocera
- No categorizado Leifheit
- No categorizado Minox
- No categorizado Ilve
- No categorizado Crosscall
- No categorizado Countryman
- No categorizado Minolta
- No categorizado Aerial
- No categorizado Delta Dore
- No categorizado Navman
- No categorizado Silver Cross
- No categorizado Victor
- No categorizado Zagg
- No categorizado ESI
- No categorizado Blumfeldt
- No categorizado SuperTooth
- No categorizado Grillmeister
- No categorizado M-e
- No categorizado Corsair
- No categorizado Edgestar
- No categorizado Orbis
- No categorizado ACE
- No categorizado For_Q
- No categorizado Schaudt
- No categorizado Avocor
- No categorizado Lanzar
- No categorizado DoorBird
- No categorizado FoodSaver
- No categorizado Vroomshoop
- No categorizado SureFlap
- No categorizado Lorex
- No categorizado GVM
- No categorizado McGregor
- No categorizado Coyote
- No categorizado Rain Bird
- No categorizado Leitz
- No categorizado Nvidia
- No categorizado Jilong
- No categorizado Teltonika
- No categorizado Vortex
- No categorizado Irritrol
- No categorizado Boneco
- No categorizado Ubiquiti Networks
- No categorizado Rapid
- No categorizado Simpson
- No categorizado Hertz
- No categorizado Exit
- No categorizado CaterChef
- No categorizado Echowell
- No categorizado Gys
- No categorizado Recaro
- No categorizado Zoom
- No categorizado Kasda
- No categorizado Marshall Electronics
- No categorizado Veho
- No categorizado Kambrook
- No categorizado EBERLE
- No categorizado Hartke
- No categorizado Nevadent
- No categorizado Plum
- No categorizado Simrad
- No categorizado Creative
- No categorizado Cellular Line
- No categorizado Jensen
- No categorizado GFI System
- No categorizado Omnitronic
- No categorizado Ctek
- No categorizado Roadstar
- No categorizado Humax
- No categorizado Eaton
- No categorizado Vaddio
- No categorizado Thrustmaster
- No categorizado G3 Ferrari
- No categorizado Berner
- No categorizado Zipper
- No categorizado Swarovski Optik
- No categorizado Gira
- No categorizado Scott
- No categorizado Caple
- No categorizado Jung
- No categorizado Mafell
- No categorizado Sachtler
- No categorizado Audiolab
- No categorizado Seagate
- No categorizado Greenworks
- No categorizado Vacmaster
- No categorizado Newstar
- No categorizado Harvia
- No categorizado Britax-Romer
- No categorizado Technicolor
- No categorizado Bravilor Bonamat
- No categorizado CyberPower
- No categorizado Huion
- No categorizado Fieldmann
- No categorizado Newline
- No categorizado Tronic
- No categorizado Blue
- No categorizado Efbe-schott
- No categorizado Brinsea
- No categorizado Genexis
- No categorizado Genelec
- No categorizado Sangean
- No categorizado Inspire
- No categorizado Gourmetmaxx
- No categorizado Basetech
- No categorizado Apart
- No categorizado Datalogic
- No categorizado Saramonic
- No categorizado Rode
- No categorizado Line 6
- No categorizado 4ms
- No categorizado Cadac
- No categorizado 4moms
- No categorizado Wolf
- No categorizado Stabila
- No categorizado Interlogix
- No categorizado Projecta
- No categorizado Eizo
- No categorizado Krontaler
- No categorizado Lyman
- No categorizado Etekcity
- No categorizado Genaray
- No categorizado Thermex
- No categorizado Zenec
- No categorizado Qualcast
- No categorizado TC Electronic
- No categorizado Cablexpert
- No categorizado Iomega
- No categorizado Ring
- No categorizado Phil And Teds
- No categorizado Tornado
- No categorizado Baby Jogger
- No categorizado Primus
- No categorizado GoDEX
- No categorizado Stelton
- No categorizado Synology
- No categorizado Mr Handsfree
- No categorizado Pattfield
- No categorizado Joovy
- No categorizado Bodum
- No categorizado DAS Audio
- No categorizado Vivitar
- No categorizado Edilkamin
- No categorizado Vestfrost
- No categorizado Elac
- No categorizado Trendnet
- No categorizado DSC
- No categorizado Leen Bakker
- No categorizado Eventide
- No categorizado Steinberg
- No categorizado Audio Pro
- No categorizado OSO
- No categorizado JLab
- No categorizado Sevenoak
- No categorizado Roxio
- No categorizado OnePlus
- No categorizado Kunft
- No categorizado Cambridge
- No categorizado Radial Engineering
- No categorizado Ewent
- No categorizado Jotul
- No categorizado Blackmagic Design
- No categorizado Mikrotik
- No categorizado Caso
- No categorizado Shoprider
- No categorizado WHALE
- No categorizado Shuttle
- No categorizado Furuno
- No categorizado HQ
- No categorizado Brita
- No categorizado Be Cool
- No categorizado Autel
- No categorizado Clage
- No categorizado Tetra
- No categorizado Fluval
- No categorizado Noveen
- No categorizado Master
- No categorizado ATen
- No categorizado Dualit
- No categorizado Cre8audio
- No categorizado Nanlite
- No categorizado Fuxtec
- No categorizado Kupper
- No categorizado Bluesound
- No categorizado Ledger
- No categorizado Contour
- No categorizado BakkerElkhuizen
- No categorizado Lupilu
- No categorizado Showtec
- No categorizado Outdoorchef
- No categorizado Boyo
- No categorizado Nobo
- No categorizado IKRA
- No categorizado Turmix
- No categorizado Fakir
- No categorizado IOttie
- No categorizado Horizon Fitness
- No categorizado Profoto
- No categorizado Laserliner
- No categorizado BOYA
- No categorizado Veritas
- No categorizado Digi
- No categorizado Verizon
- No categorizado Astralpool
- No categorizado Ultimate
- No categorizado ADATA
- No categorizado XPG
- No categorizado Valco Baby
- No categorizado Trio Lighting
- No categorizado Integra
- No categorizado Upo
- No categorizado Vitamix
- No categorizado Metra
- No categorizado Xtorm
- No categorizado Blade
- No categorizado Hestan
- No categorizado Rio
- No categorizado Cadel
- No categorizado Baxi
- No categorizado ThinkFun
- No categorizado Ipevo
- No categorizado Rommer
- No categorizado Mophie
- No categorizado Fibaro
- No categorizado Princeton Tec
- No categorizado Iget
- No categorizado Revox
- No categorizado Emtec
- No categorizado Ranex
- No categorizado Russound
- No categorizado Truper
- No categorizado Easy Home
- No categorizado ISDT
- No categorizado Abac
- No categorizado Stannah
- No categorizado Celly
- No categorizado Kindermann
- No categorizado Comica
- No categorizado CRUX
- No categorizado Tommee Tippee
- No categorizado Globo
- No categorizado Conceptronic
- No categorizado ZLine
- No categorizado EverFocus
- No categorizado Watson
- No categorizado Fusion
- No categorizado Eurolite
- No categorizado Sebo
- No categorizado Audient
- No categorizado Heller
- No categorizado Geemarc
- No categorizado Vornado
- No categorizado Adesso
- No categorizado Hegel
- No categorizado Paradigm
- No categorizado Infantino
- No categorizado RGBlink
- No categorizado Gefen
- No categorizado C3
- No categorizado Nexa
- No categorizado Reebok
- No categorizado EMSA
- No categorizado Waldbeck
- No categorizado Natuzzi
- No categorizado Grunkel
- No categorizado Satel
- No categorizado Scosche
- No categorizado Bazooka
- No categorizado K&K Sound
- No categorizado Vivotek
- No categorizado Dutchbone
- No categorizado MyPhone
- No categorizado Fanvil
- No categorizado Noise Engineering
- No categorizado PAC
- No categorizado Wentronic
- No categorizado Peerless
- No categorizado RAVPower
- No categorizado Mooer
- No categorizado Hooker
- No categorizado Polti
- No categorizado Dynaudio
- No categorizado Terratec
- No categorizado IHome
- No categorizado August
- No categorizado Atomos
- No categorizado Dormakaba
- No categorizado Adder
- No categorizado Gitzo
- No categorizado M-Audio
- No categorizado SeaLife
- No categorizado Infinity
- No categorizado DBX
- No categorizado Nesco
- No categorizado Wago
- No categorizado AIC
- No categorizado ECS
- No categorizado Concept2
- No categorizado Cleanmaxx
- No categorizado Dali
- No categorizado Brydge
- No categorizado Selec
- No categorizado Aiphone
- No categorizado Tivoli Audio
- No categorizado Senal
- No categorizado JETI
- No categorizado Waves
- No categorizado EQ3
- No categorizado Karlik
- No categorizado Comark
- No categorizado Homematic IP
- No categorizado Lervia
- No categorizado Coline
- No categorizado N8WERK
- No categorizado Petri
- No categorizado Scancool
- No categorizado Satechi
- No categorizado REV
- No categorizado Skullcandy
- No categorizado Hansgrohe
- No categorizado Masport
- No categorizado Jamo
- No categorizado NZXT
- No categorizado Veripart
- No categorizado Grizzly
- No categorizado Rocktrail
- No categorizado 4smarts
- No categorizado ILive
- No categorizado Learning Resources
- No categorizado Xaoc
- No categorizado Beyerdynamic
- No categorizado SVAT
- No categorizado Oppo
- No categorizado Syma
- No categorizado Victrola
- No categorizado Lanberg
- No categorizado Friedland
- No categorizado Kopul
- No categorizado AENO
- No categorizado Interstuhl
- No categorizado Proaim
- No categorizado Coleman
- No categorizado Bora
- No categorizado Magic Care
- No categorizado Raclet
- No categorizado Butler
- No categorizado Intenso
- No categorizado Weishaupt
- No categorizado Hammond
- No categorizado Testo
- No categorizado Glock
- No categorizado Revo
- No categorizado Baby Lock
- No categorizado Linn
- No categorizado Martin Logan
- No categorizado Quantum
- No categorizado Elta
- No categorizado Iluv
- No categorizado Monitor Audio
- No categorizado Vorago
- No categorizado REMKO
- No categorizado Anton/Bauer
- No categorizado Monoprice
- No categorizado Croozer
- No categorizado TELEX
- No categorizado Dynamic
- No categorizado Sauter
- No categorizado Promethean
- No categorizado HyperIce
- No categorizado Home Easy
- No categorizado Clean Air Optima
- No categorizado Chipolino
- No categorizado Munchkin
- No categorizado Solo
- No categorizado Vitalmaxx
- No categorizado Yorkville
- No categorizado Nxg
- No categorizado DPA
- No categorizado Cocraft
- No categorizado Diana
- No categorizado Tandberg Data
- No categorizado Fostex
- No categorizado Toyotomi
- No categorizado GA.MA
- No categorizado Viridian
- No categorizado Plustek
- No categorizado Prowise
- No categorizado Impact
- No categorizado Areca
- No categorizado Mousetrapper
- No categorizado SKROSS
- No categorizado Sikkens
- No categorizado DEXP
- No categorizado Burris
- No categorizado Lynx
- No categorizado Barazza
- No categorizado Proel
- No categorizado FBT
- No categorizado Tiptel
- No categorizado Roccat
- No categorizado Thermor
- No categorizado Edge
- No categorizado Endorphin.es
- No categorizado Crofton
- No categorizado Deutz
- No categorizado Optimum
- No categorizado FIMI
- No categorizado Flavel
- No categorizado Bravilor
- No categorizado HQ Power
- No categorizado Bracketron
- No categorizado Solid State Logic
- No categorizado Pointer
- No categorizado XYZprinting
- No categorizado HyperX
- No categorizado Computherm
- No categorizado Edision
- No categorizado Carmen
- No categorizado MTM
- No categorizado Broan
- No categorizado Avidsen
- No categorizado Metapace
- No categorizado Cougar
- No categorizado Zeiss
- No categorizado Neets
- No categorizado NAV-TV
- No categorizado Wooden Camera
- No categorizado Maclaren
- No categorizado Stamina
- No categorizado AdHoc
- No categorizado Chief
- No categorizado SEH
- No categorizado AudioQuest
- No categorizado Eurochron
- No categorizado Powerblade
- No categorizado HiFi ROSE
- No categorizado Hayter
- No categorizado Furrion
- No categorizado Pinolino
- No categorizado Cecotec
- No categorizado Antari
- No categorizado Gianni Ferrari
- No categorizado OSD Audio
- No categorizado WMD
- No categorizado Andover
- No categorizado Arctic Cooling
- No categorizado Beafon
- No categorizado Maruyama
- No categorizado SPC
- No categorizado Stabo
- No categorizado Blackstar
- No categorizado Oreck
- No categorizado Ergotron
- No categorizado Stairville
- No categorizado Zepter
- No categorizado Crestron
- No categorizado Giordani
- No categorizado RME
- No categorizado Black Lion Audio
- No categorizado Cowon
- No categorizado Soundstream
- No categorizado Crayola
- No categorizado Fischer
- No categorizado Xoro
- No categorizado Medel
- No categorizado Livington
- No categorizado REVITIVE
- No categorizado Herkules
- No categorizado CTOUCH
- No categorizado Instant
- No categorizado Adastra
- No categorizado Gabor
- No categorizado Konig & Meyer
- No categorizado Meister Craft
- No categorizado Meade
- No categorizado Sagemcom
- No categorizado Yeastar
- No categorizado Laserworld
- No categorizado Billow
- No categorizado Chuango
- No categorizado Kelty
- No categorizado West Elm
- No categorizado Block
- No categorizado Keter
- No categorizado Ozone
- No categorizado Truelife
- No categorizado Bikemate
- No categorizado Klavis
- No categorizado Garden Lights
- No categorizado Monster
- No categorizado ORNO
- No categorizado Jabsco
- No categorizado Dash
- No categorizado Yukon
- No categorizado Foxconn
- No categorizado Segway
- No categorizado Icy Dock
- No categorizado IMC Toys
- No categorizado Baby Brezza
- No categorizado Make Noise
- No categorizado Toolcraft
- No categorizado Telstra
- No categorizado TeachLogic
- No categorizado Maytronics
- No categorizado ASSA ABLOY
- No categorizado Sole Fitness
- No categorizado Power Dynamics
- No categorizado Lumag
- No categorizado Charge Amps
- No categorizado Berker
- No categorizado Eufab
- No categorizado Manfrotto
- No categorizado Crucial
- No categorizado Snom
- No categorizado RIDGID
- No categorizado Premier
- No categorizado Ibm
- No categorizado Unilux
- No categorizado Shokz
- No categorizado Citronic
- No categorizado Pontec
- No categorizado Maxell
- No categorizado Cosatto
- No categorizado Weasy
- No categorizado Aerotec
- No categorizado Atlas
- No categorizado Datacard
- No categorizado Dreamgear
- No categorizado ZYCOO
- No categorizado Macrom
- No categorizado Kontakt Chemie
- No categorizado Purell
- No categorizado Riccar
- No categorizado Contax
- No categorizado OpenVox
- No categorizado Electro Harmonix
- No categorizado Erica Synths
- No categorizado SkyRC
- No categorizado Atdec
- No categorizado Grandstream
- No categorizado Batavia
- No categorizado Klarfit
- No categorizado Proxxon
- No categorizado Kalorik
- No categorizado Mercury
- No categorizado Gutfels
- No categorizado Bruynzeel
- No categorizado Toro
- No categorizado Definitive Technology
- No categorizado Fender
- No categorizado Gardenline
- No categorizado MSpa
- No categorizado View Quest
- No categorizado Drayton
- No categorizado Crane
- No categorizado Formuler
- No categorizado Maximum
- No categorizado Eden
- No categorizado Vantec
- No categorizado Sonnet
- No categorizado Oertli
- No categorizado UX
- No categorizado Moog
- No categorizado Nerf
- No categorizado Gamdias
- No categorizado KidKraft
- No categorizado SPL
- No categorizado Westfalia
- No categorizado Monacor
- No categorizado Metrel
- No categorizado Multimetrix
- No categorizado Solid
- No categorizado NUK
- No categorizado Ruger
- No categorizado Hubelino
- No categorizado Aputure
- No categorizado Gerni
- No categorizado PCE
- No categorizado Baby Annabell
- No categorizado Warm Audio
- No categorizado Brandson
- No categorizado Heatit
- No categorizado Endress
- No categorizado Deaf Bonce
- No categorizado ProForm
- No categorizado UTEPO
- No categorizado Purpleline
- No categorizado Lindell Audio
- No categorizado ARRI
- No categorizado Max Pro
- No categorizado Think Tank
- No categorizado Portech
- No categorizado Twelve South
- No categorizado Lec
- No categorizado Geomag
- No categorizado LTC
- No categorizado Martin
- No categorizado Koala
- No categorizado Drawmer
- No categorizado Audeze
- No categorizado Blue Sky
- No categorizado Dunlop
- No categorizado Valeo
- No categorizado Noxon
- No categorizado GW Instek
- No categorizado Galanz
- No categorizado Velbus
- No categorizado Babyzen
- No categorizado Logilink
- No categorizado IQAir
- No categorizado Sanus Systems
- No categorizado ColorKey
- No categorizado Tormatic
- No categorizado After Later Audio
- No categorizado Aqara
- No categorizado Verbatim
- No categorizado Energizer
- No categorizado IXS
- No categorizado Samlex
- No categorizado Navionics
- No categorizado AirTurn
- No categorizado Zalman
- No categorizado Turbo Air
- No categorizado Leatherman
- No categorizado Havis
- No categorizado Orava
- No categorizado Horizon
- No categorizado Gastronoma
- No categorizado Moxa
- No categorizado Ultimate Support
- No categorizado POLARIS
- No categorizado Rösle
- No categorizado Smart-AVI
- No categorizado Osram
- No categorizado StarTech.com
- No categorizado AXI
- No categorizado Inter-Tech
- No categorizado Thomann
- No categorizado Holzmann
- No categorizado EMG
- No categorizado Bicker Elektronik
- No categorizado Iadea
- No categorizado Blizzard
- No categorizado Geneva
- No categorizado SIIG
- No categorizado Realme
- No categorizado Advantech
- No categorizado PSSO
- No categorizado Levenhuk
- No categorizado SIG Sauer
- No categorizado Merkel
- No categorizado Patching Panda
- No categorizado Harley Benton
- No categorizado Biohort
- No categorizado Globe
- No categorizado Rossi
- No categorizado IOGEAR
- No categorizado Hercules
- No categorizado Grace Design
- No categorizado Contour Design
- No categorizado Heckler Design
- No categorizado Buzz Rack
- No categorizado Cruz
- No categorizado Nanuk
- No categorizado Digital Watchdog
- No categorizado Sonifex
- No categorizado Riviera And Bar
- No categorizado Apelson
- No categorizado EcoFlow
- No categorizado Kreiling
- No categorizado Xantech
- No categorizado Scanstrut
- No categorizado Kohler
- No categorizado Safco
- No categorizado Xunzel
- No categorizado Fein
- No categorizado Oklahoma Sound
- No categorizado Thames & Kosmos
- No categorizado Kali Audio
- No categorizado Audioengine
- No categorizado Fortia
- No categorizado Moen
- No categorizado IFi Audio
- No categorizado Babysense
- No categorizado Namco Bandai Games
- No categorizado Witt
- No categorizado Revel
- No categorizado Sealy
- No categorizado Ferguson
- No categorizado Wet Sounds
- No categorizado CRU
- No categorizado Avantone Pro
- No categorizado Sanitaire
- No categorizado Umarex
- No categorizado Televés
- No categorizado AbleNet
- No categorizado Exalux
- No categorizado IBasso
- No categorizado Bolt
- No categorizado Leap Frog
- No categorizado Eissound
- No categorizado Hughes & Kettner
- No categorizado Manley
- No categorizado JOBY
- No categorizado Micro Matic
- No categorizado Audix
- No categorizado MEE Audio
- No categorizado DAP Audio
- No categorizado Steiner
- No categorizado Kingston
- No categorizado NordicTrack
- No categorizado Burigotto
- No categorizado Redmond
- No categorizado Norton Clipper
- No categorizado Extron
- No categorizado KanexPro
- No categorizado Blustream
- No categorizado Avocent
- No categorizado SVS
- No categorizado Franklin
- No categorizado RTS
- No categorizado Ontech
- No categorizado Koss
- No categorizado Swingline
- No categorizado Kwikset
- No categorizado Infomir
- No categorizado RaySafe
- No categorizado Di4
- No categorizado Hohner
- No categorizado Khind
- No categorizado Ashly
- No categorizado Shelly
- No categorizado Husky
- No categorizado Philos
- No categorizado Legamaster
- No categorizado Antec
- No categorizado Elmo
- No categorizado Siemon
- No categorizado Block & Block
- No categorizado Brondell
- No categorizado NutriBullet
- No categorizado Four Hands
- No categorizado Oregon Scientific
- No categorizado Oben
- No categorizado ASA
- No categorizado XGIMI
- No categorizado Thronmax
- No categorizado Axkid
- No categorizado Botex
- No categorizado Intellinet
- No categorizado Maxsa
- No categorizado Park Tool
- No categorizado Ankarsrum
- No categorizado MTD
- No categorizado Dangerous Music
- No categorizado Etymotic
- No categorizado Foster
- No categorizado Everdure
- No categorizado ELO
- No categorizado Heidemann
- No categorizado OneTouch
- No categorizado Medeli
- No categorizado Superrollo
- No categorizado Goldtouch
- No categorizado Gamewright
- No categorizado Kerbl
- No categorizado Reflexion
- No categorizado Roidmi
- No categorizado Braun Phototechnik
- No categorizado Muller
- No categorizado Scala
- No categorizado SXT
- No categorizado Seecode
- No categorizado Thomas
- No categorizado Duronic
- No categorizado Rugged Geek
- No categorizado Nubert
- No categorizado Skymaster
- No categorizado Lancom
- No categorizado Dorr
- No categorizado PATLITE
- No categorizado Minn Kota
- No categorizado Lian Li
- No categorizado Match
- No categorizado Vocopro
- No categorizado Gardol
- No categorizado Helix
- No categorizado TFA Dostmann
- No categorizado Werma
- No categorizado Walrus Audio
- No categorizado Durable
- No categorizado Zenza Bronica
- No categorizado Spypoint
- No categorizado Greisinger
- No categorizado Ziehl
- No categorizado VAIS
- No categorizado Revlon
- No categorizado Glide Gear
- No categorizado Enovate
- No categorizado Lofrans
- No categorizado Winegard
- No categorizado Pigtronix
- No categorizado ProTeam
- No categorizado Wagner SprayTech
- No categorizado Libec
- No categorizado Hoshizaki
- No categorizado Pardini
- No categorizado Beha-Amprobe
- No categorizado Soul
- No categorizado Laney
- No categorizado Compex
- No categorizado Theragun
- No categorizado Plantiflor
- No categorizado LAS
- No categorizado Redrock Micro
- No categorizado Motu
- No categorizado Kata
- No categorizado Minix
- No categorizado Lazer
- No categorizado EarthQuaker Devices
- No categorizado AVer
- No categorizado Emga
- No categorizado Devialet
- No categorizado USAopoly
- No categorizado Igloohome
- No categorizado Kenko
- No categorizado Zennio
- No categorizado Vixen
- No categorizado B-tech
- No categorizado Praktica
- No categorizado WAGAN
- No categorizado Elinchrom
- No categorizado Kopp
- No categorizado Boori
- No categorizado Universal Audio
- No categorizado Hasselblad
- No categorizado Madrix
- No categorizado ResMed
- No categorizado Q Acoustics
- No categorizado Spacedec
- No categorizado Auray
- No categorizado Bontempi
- No categorizado Furman
- No categorizado Summer Infant
- No categorizado Cooper & Quint
- No categorizado Infasecure
- No categorizado Thinkware
- No categorizado Xplora
- No categorizado Eonon
- No categorizado SMC
- No categorizado Crimson
- No categorizado Ibico
- No categorizado OXO Good Grips
- No categorizado Exit Toys
- No categorizado Lifespan
- No categorizado Triton
- No categorizado Profizelt24
- No categorizado YSI
- No categorizado Paulmann
- No categorizado Playtive
- No categorizado Martin Audio
- No categorizado Schertler
- No categorizado Teradek
- No categorizado Kern
- No categorizado Sissel
- No categorizado Kunath
- No categorizado Vimar
- No categorizado Penclic
- No categorizado SolarEdge
- No categorizado ViewCast
- No categorizado Crown
- No categorizado Kogan
- No categorizado Wolfcraft
- No categorizado Tennsco
- No categorizado FireKing
- No categorizado Tannoy
- No categorizado Ocean Matrix
- No categorizado Novus
- No categorizado Dedra
- No categorizado Getac
- No categorizado Arebos
- No categorizado Kreg
- No categorizado Morningstar
- No categorizado DMax
- No categorizado Lenoxx
- No categorizado Speco Technologies
- No categorizado Backyard Discovery
- No categorizado Minuteman
- No categorizado Brady
- No categorizado Ortofon
- No categorizado Cameo
- No categorizado ZKTeco
- No categorizado Mega
- No categorizado Esperanza
- No categorizado PowerXL
- No categorizado Star Micronics
- No categorizado Kemo
- No categorizado Tamron
- No categorizado Woodland Scenics
- No categorizado Chapin
- No categorizado Gloria
- No categorizado J. Rockett Audio Designs
- No categorizado Pancontrol
- No categorizado Satisfyer
- No categorizado Hämmerli
- No categorizado Verto
- No categorizado Maxcom
- No categorizado Soma
- No categorizado Posiflex
- No categorizado SRS
- No categorizado Little Giant
- No categorizado Signature
- No categorizado Point 65
- No categorizado Avantree
- No categorizado Akuvox
- No categorizado LYYT
- No categorizado Jay-tech
- No categorizado Old Blood Noise
- No categorizado Vulcan
- No categorizado CradlePoint
- No categorizado GAO
- No categorizado Rovo Kids
- No categorizado Uni-T
- No categorizado Dension
- No categorizado Antelope Audio
- No categorizado Kugoo
- No categorizado Brinno
- No categorizado Venom
- No categorizado H-Tronic
- No categorizado CE Labs
- No categorizado Mean Well
- No categorizado Legrand
- No categorizado Digium
- No categorizado Giardino
- No categorizado Mulex
- No categorizado Panduit
- No categorizado Raymarine
- No categorizado Novation
- No categorizado I.safe Mobile
- No categorizado Socomec
- No categorizado System Sensor
- No categorizado San Jamar
- No categorizado REL Acoustics
- No categorizado IPort
- No categorizado X-Rite
- No categorizado Wetelux
- No categorizado Merax
- No categorizado GermGuardian
- No categorizado R-Go Tools
- No categorizado Urbanista
- No categorizado SLV
- No categorizado Sagitter
- No categorizado Rainbow
- No categorizado Duracell
- No categorizado Riello
- No categorizado Gagato
- No categorizado Traeger
- No categorizado General
- No categorizado Ooni
- No categorizado ECTIVE
- No categorizado Elgato
- No categorizado Gymform
- No categorizado Ebro
- No categorizado Doffler
- No categorizado Tzumi
- No categorizado BERTSCHAT
- No categorizado Schumacher
- No categorizado Michael Todd Beauty
- No categorizado Testec
- No categorizado Cygnett
- No categorizado Germania
- No categorizado Victorio
- No categorizado Platinum
- No categorizado Foreo
- No categorizado Trimble
- No categorizado JAYS
- No categorizado Playtive Junior
- No categorizado Intertechno
- No categorizado Parklands
- No categorizado Avid
- No categorizado Vipack
- No categorizado Helios
- No categorizado Schwaiger
- No categorizado Consul
- No categorizado EKO
- No categorizado BIG
- No categorizado Emeril Lagasse
- No categorizado SureFire
- No categorizado POGS
- No categorizado Graflex
- No categorizado Coolaroo
- No categorizado Insta360
- No categorizado Hikmicro
- No categorizado Wurth
- No categorizado Ketron
- No categorizado Mebus
- No categorizado Kenton
- No categorizado Cypress
- No categorizado Foliatec
- No categorizado Mauser
- No categorizado Silhouette
- No categorizado South Shore
- No categorizado Discovery
- No categorizado T4E
- No categorizado Speck
- No categorizado Generation
- No categorizado Iseki
- No categorizado 8BitDo
- No categorizado MOZA
- No categorizado ModeCom
- No categorizado Ecler
- No categorizado Turbosound
- No categorizado Phase One
- No categorizado Röhm
- No categorizado Ulanzi
- No categorizado Bluetti
- No categorizado Tineco
- No categorizado Anova
- No categorizado Viscount
- No categorizado Hurricane
- No categorizado JennAir
- No categorizado Newland
- No categorizado DAB
- No categorizado Anex
- No categorizado Flama
- No categorizado Pawa
- No categorizado V-Tac
- No categorizado LERAN
- No categorizado Majella
- No categorizado GMB Audio
- No categorizado Ashdown Engineering
- No categorizado Century
- No categorizado EQ-3
- No categorizado Unger
- No categorizado Naim
- No categorizado Inverto
- No categorizado Special-T
- No categorizado Ygnis
- No categorizado Esotec
- No categorizado True & Tidy
- No categorizado NovaStar
- No categorizado Petkit
- No categorizado Icon
- No categorizado Fuzzix
- No categorizado Kitchen Brains
- No categorizado Challenge Xtreme
- No categorizado Best
- No categorizado Flycam
- No categorizado NetAlly
- No categorizado Triax
- No categorizado Peltor
- No categorizado JAR Systems
- No categorizado Global
- No categorizado Moleskine
- No categorizado Bytecc
- No categorizado Strex
- No categorizado Xlyne
- No categorizado Premier Mounts
- No categorizado One Stop Systems
- No categorizado Cool Maker
- No categorizado PeakTech
- No categorizado Neo
- No categorizado EVOline
- No categorizado Mtx Audio
- No categorizado Ursus Trotter
- No categorizado DoughXpress
- No categorizado Ground Zero
- No categorizado Aquatic AV
- No categorizado Parasound
- No categorizado MSR
- No categorizado Keurig
- No categorizado Gravity
- No categorizado Cabstone
- No categorizado SPT
- No categorizado DB Technologies
- No categorizado T.I.P.
- No categorizado Promate
- No categorizado Sonel
- No categorizado Berger & Schröter
- No categorizado Tru Components
- No categorizado Step2
- No categorizado Crystal Quest
- No categorizado Emko
- No categorizado Mistral
- No categorizado Pit Boss
- No categorizado Needit
- No categorizado MiPow
- No categorizado GoldenEar Technology
- No categorizado Colt
- No categorizado Elite Screens
- No categorizado Sungrow
- No categorizado Quadro
- No categorizado Ultron
- No categorizado Choice
- No categorizado Roswell
- No categorizado King Craft
- No categorizado FOX ESS
- No categorizado Airman
- No categorizado Cascade Audio Engineering
- No categorizado B-Speech
- No categorizado Apa
- No categorizado Vanish
- No categorizado Nostalgia
- No categorizado Grosfillex
- No categorizado Solplanet
- No categorizado Platinet
- No categorizado Santos
- No categorizado Entes
- No categorizado Evoc
- No categorizado Versare
- No categorizado Enphase
- No categorizado Tractive
- No categorizado SpeakerCraft
- No categorizado Celexon
- No categorizado Epcom
- No categorizado EVOLVEO
- No categorizado Kanto
- No categorizado Prixton
- No categorizado ZeeVee
- No categorizado Primera
- No categorizado Siku
- No categorizado Viatek
- No categorizado ADDAC System
- No categorizado Simplicity
- No categorizado Doomoo
- No categorizado MBZ
- No categorizado Davey
- No categorizado Mettler
- No categorizado Metalux
- No categorizado Heitech
- No categorizado Potenza
- No categorizado LOQED
- No categorizado Hatco
- No categorizado Fulgor Milano
- No categorizado KONFTEL
- No categorizado Canicom
- No categorizado EGO
- No categorizado Mitsai
- No categorizado Selfsat
- No categorizado Leef
- No categorizado Tusa
- No categorizado Hovicon
- No categorizado Starlyf
- No categorizado Kramer
- No categorizado RCBS
- No categorizado American BioTech Supply
- No categorizado Lagrange
- No categorizado Noris
- No categorizado JANDY
- No categorizado KS Tools
- No categorizado Schmidt & Bender
- No categorizado Mesa Boogie
- No categorizado Improv
- No categorizado InLine
- No categorizado LandRoller
- No categorizado Wegman
- No categorizado Lockncharge
- No categorizado Merlin
- No categorizado Standard Horizon
- No categorizado V7
- No categorizado Goal Zero
- No categorizado HealthPostures
- No categorizado Dreadbox
- No categorizado Joranalogue
- No categorizado CYP
- No categorizado Heaven Fresh
- No categorizado Lutec
- No categorizado Champion Sports
- No categorizado Molotow
- No categorizado Herlag
- No categorizado Dux
- No categorizado FALLER
- No categorizado Miditech
- No categorizado SE Electronics
- No categorizado TTM
- No categorizado Paw Patrol
- No categorizado ISi
- No categorizado LELO
- No categorizado AudioControl
- No categorizado Apricorn
- No categorizado Timbersled
- No categorizado Mermade
- No categorizado MXR
- No categorizado SKLZ
- No categorizado Herma
- No categorizado Cyrus
- No categorizado BWT
- No categorizado Syrp
- No categorizado Ugolini
- No categorizado Cosina
- No categorizado Heckler & Koch
- No categorizado Whistler
- No categorizado Twisper
- No categorizado Suevia
- No categorizado Manitowoc
- No categorizado Palmer
- No categorizado J5create
- No categorizado Lund
- No categorizado Hushmat
- No categorizado Xigmatek
- No categorizado Tema
- No categorizado Intellijel
- No categorizado ALM
- No categorizado Topaz
- No categorizado Toddy
- No categorizado Aicon
- No categorizado Astell&Kern
- No categorizado Doepfer
- No categorizado Fun Generation
- No categorizado Xvive
- No categorizado Karma
- No categorizado TV One
- No categorizado Berkel
- No categorizado Empress Effects
- No categorizado Dreame
- No categorizado Hugo Muller
- No categorizado Vinci
- No categorizado Jordan
- No categorizado Duromax
- No categorizado DataComm
- No categorizado Powercube
- No categorizado Kasp
- No categorizado Dimavery
- No categorizado Hanwha
- No categorizado WestBend
- No categorizado Mr Coffee
- No categorizado Sherlock
- No categorizado SEA-PRO
- No categorizado Livarno Lux
- No categorizado Omiindustriies
- No categorizado Weltevree
- No categorizado Phoenix Contact
- No categorizado AMS Neve
- No categorizado LVSUN
- No categorizado Aston Microphones
- No categorizado Netsys
- No categorizado Alfi
- No categorizado Gtech
- No categorizado Polarlite
- No categorizado Companion
- No categorizado Mr. Beams
- No categorizado Morphor
- No categorizado Lapp
- No categorizado XO
- No categorizado PcDuino
- No categorizado LECO
- No categorizado Maretron
- No categorizado Hortus
- No categorizado Razorri
- No categorizado Fetch
- No categorizado Zoetis
- No categorizado Prem-i-air
- No categorizado NWS
- No categorizado GAM
- No categorizado Knog
- No categorizado Scale Computing
- No categorizado Media-tech
- No categorizado Naturn Living
- No categorizado Aeotec
- No categorizado Catlink
- No categorizado FitterFirst
- No categorizado Raveland
- No categorizado Mr. Heater
- No categorizado Welltech
- No categorizado Trumeter
- No categorizado Seidio
- No categorizado Sincreative
- No categorizado JDC
- No categorizado HammerSmith
- No categorizado Hidrate
- No categorizado Sonicware
- No categorizado Nexibo
- No categorizado Jolin
- No categorizado MoTip
- No categorizado Stenda
- No categorizado Pro-Lift
- No categorizado HIOAZO
- No categorizado Malstrom
- No categorizado Laserluchs
- No categorizado Powersoft
- No categorizado Casetastic
- No categorizado UClear
- No categorizado BikeLogger
- No categorizado Tor Rey
- No categorizado Momo Design
- No categorizado Esdec
- No categorizado Ruark Audio
- No categorizado Neewer
- No categorizado AJH Synth
- No categorizado LifeStraw
- No categorizado Lincoln Electric
- No categorizado Toolit
- No categorizado Egnater
- No categorizado DutchOne
- No categorizado Feitian
- No categorizado Cranborne Audio
- No categorizado Ergie
- No categorizado Reltech
- No categorizado Armcross
- No categorizado Focus Electrics
- No categorizado Huntleigh
- No categorizado Beeletix
- No categorizado Gehmann
- No categorizado Batronix
- No categorizado Franzis
- No categorizado Gridbyt
- No categorizado TDK-Lambda
- No categorizado LONQ
- No categorizado Em-Trak
- No categorizado Wonky Monkey
- No categorizado Dresden Elektronik
- No categorizado Atmel
- No categorizado Flavour Blaster
- No categorizado Esoteric
- No categorizado SmartAVI
- No categorizado EPH Elektronik
- No categorizado InfiRay
- No categorizado Best Service
- No categorizado Markbass
- No categorizado IMG Stage Line
- No categorizado IMAC
- No categorizado Metz Connect
- No categorizado MGL Avionics
- No categorizado Eikon
- No categorizado Casablanca
- No categorizado Nemco
- No categorizado Wireless Solution
- No categorizado Beverage-Air
- No categorizado Sparco
- No categorizado Barber Tech
- No categorizado Estella
- No categorizado EarFun
- No categorizado Oehlbach
- No categorizado Minkels
- No categorizado Kipor
- No categorizado Lenmar
- No categorizado HMS Premium
- No categorizado Arduino
- No categorizado Ave Six
- No categorizado Bestar
- No categorizado Pelco
- No categorizado Gardigo
- No categorizado Highpoint
- No categorizado Puls Dimension
- No categorizado Studiologic
- No categorizado Fischer Amps
- No categorizado CHINT
- No categorizado Sirus
- No categorizado Digitech
- No categorizado Leviton
- No categorizado Chauvin Arnoux
- No categorizado Gretsch
- No categorizado Pentacon
- No categorizado Winia
- No categorizado Atlas Sound
- No categorizado Bolsey
- No categorizado Louis Tellier
- No categorizado EtiamPro
- No categorizado Simeo
- No categorizado Baracuda
- No categorizado Kstar
- No categorizado BeSafe
- No categorizado Air Guard
- No categorizado Neutrik
- No categorizado MediaMatrix
- No categorizado ESX
- No categorizado Anywhere Cart
- No categorizado Tuur
- No categorizado ONE Smart Control
- No categorizado Megger
- No categorizado Edelkrone
- No categorizado OBSBOT
- No categorizado InSinkErator
- No categorizado AREXX
- No categorizado Artusi
- No categorizado Gossen Metrawatt
- No categorizado Omnires
- No categorizado IVT
- No categorizado Elite Force
- No categorizado JK Audio
- No categorizado Piko
- No categorizado Lifan
- No categorizado Jomox
- No categorizado Burley
- No categorizado Lexicon
- No categorizado Graphite
- No categorizado Icarus Blue
- No categorizado Command
- No categorizado IRIS
- No categorizado Neno
- No categorizado Rigol
- No categorizado Starburst
- No categorizado Futurelight
- No categorizado AVPro Edge
- No categorizado Fluance
- No categorizado PCE Instruments
- No categorizado Garden Place
- No categorizado Rinnai
- No categorizado Moldex
- No categorizado Cudy
- No categorizado MaximaVida
- No categorizado Firefriend
- No categorizado DOD
- No categorizado LightZone
- No categorizado KRK
- No categorizado Robinhood
- No categorizado Bliss Outdoors
- No categorizado Fontiso
- No categorizado Varytec
- No categorizado Altra
- No categorizado Omnilux
- No categorizado Socket Mobile
- No categorizado Enermax
- No categorizado Quartet
- No categorizado Heitronic
- No categorizado Shadow
- No categorizado IP-COM
- No categorizado Calligaris .com
- No categorizado Comtek
- No categorizado Fishman
- No categorizado Tams Elektronik
- No categorizado Digital Juice
- No categorizado Eschenbach
- No categorizado Neumärker
- No categorizado ASM
- No categorizado Bretford
- No categorizado Elektron
- No categorizado Ltech
- No categorizado Kiev
- No categorizado RetroSound
- No categorizado PowerBass
- No categorizado Caroline
- No categorizado Zomo
- No categorizado VAIS Technology
- No categorizado NEO Tools
- No categorizado Synco
- No categorizado Buchla & TipTop Audio
- No categorizado Kiloview
- No categorizado Pyramid
- No categorizado Maico
- No categorizado Lindy
- No categorizado SHX
- No categorizado On-Q
- No categorizado Govee
- No categorizado Sirius
- No categorizado SetonixSynth
- No categorizado Horex
- No categorizado Inno-Hit
- No categorizado AvaValley
- No categorizado INTIMINA
- No categorizado Monzana
- No categorizado FCC BBQ
- No categorizado Auto XS
- No categorizado Toomax
- No categorizado Aqua Marina
- No categorizado Hameg
- No categorizado Greemotion
- No categorizado Winter Modular
- No categorizado Salewa
- No categorizado FED
- No categorizado Platinum Tools
- No categorizado Synamodec
- No categorizado Grotime
- No categorizado Pico Macom
- No categorizado RadonTec
- No categorizado Katrin
- No categorizado TDE Instruments
- No categorizado Kendau
- No categorizado Kisag
- No categorizado NUX
- No categorizado Coxreels
- No categorizado Morley
- No categorizado Overade
- No categorizado Liemke
- No categorizado Copco
- No categorizado Vanson
- No categorizado Canyon
- No categorizado Carcomm
- No categorizado Style Me Up
- No categorizado Swedish Posture
- No categorizado JIMMY
- No categorizado Melnor
- No categorizado CDVI
- No categorizado Excalibur
- No categorizado Sôlt
- No categorizado Holman
- No categorizado HomePilot
- No categorizado Leaptel
- No categorizado Lifenaxx
- No categorizado Powertec
- No categorizado Waterbird
- No categorizado Joy-it
- No categorizado Dreambaby
- No categorizado AOpen
- No categorizado Angler
- No categorizado GP
- No categorizado Akrobat
- No categorizado Casaria
- No categorizado Techno Line
- No categorizado Selleys
- No categorizado WindFall
- No categorizado Ameristep
- No categorizado Rikon
- No categorizado KM-fit
- No categorizado X Rocker
- No categorizado Mircom
- No categorizado ESUN
- No categorizado TSC
- No categorizado Durex
- No categorizado Ravanson
- No categorizado Wachendorff
- No categorizado AeroCool
- No categorizado Klein Tools
- No categorizado Vantage Point
- No categorizado Jokari
- No categorizado BeeSecure
- No categorizado MantelMount
- No categorizado Unicol
- No categorizado Lasita Maja
- No categorizado Meccano
- No categorizado Parallels
- No categorizado Oatey
- No categorizado QUIO
- No categorizado Fisher
- No categorizado Gretsch Guitars
- No categorizado Banoch
- No categorizado XP-PEN
- No categorizado Atmotube
- No categorizado Sun Pumps
- No categorizado Electrify
- No categorizado Leatt
- No categorizado Bleep Labs
- No categorizado FontaFit
- No categorizado Gossmann
- No categorizado Comatec
- No categorizado Jonard Tools
- No categorizado WEG
- No categorizado Atech Flash Technology
- No categorizado AutoParkTime
- No categorizado Hudora
- No categorizado Ernitec
- No categorizado Facal
- No categorizado Planet Audio
- No categorizado Datacolor
- No categorizado Silicon Power
- No categorizado Sabrent
- No categorizado Aim TTi
- No categorizado JAXY
- No categorizado WARN
- No categorizado Aarke
- No categorizado TikkTokk
- No categorizado Roco
- No categorizado Flexson
- No categorizado Camec
- No categorizado Wibrain
- No categorizado Rolly Toys
- No categorizado Deditec
- No categorizado Level Mount
- No categorizado Teenage Engineering
- No categorizado Elipson
- No categorizado STANDIVARIUS
- No categorizado CommScope
- No categorizado Orange
- No categorizado Extralife Instruments
- No categorizado Genki Instruments
- No categorizado Industrial Music Electronics
- No categorizado Mauser Sitzkultur
- No categorizado Accezz
- No categorizado Create
- No categorizado A4 Tech
- No categorizado Full Boar
- No categorizado Zedar
- No categorizado Yli Electronic
- No categorizado Dals
- No categorizado Bulman
- No categorizado TOOLMATE
- No categorizado SleepPro
- No categorizado Muama
- No categorizado Lepu Medical
- No categorizado Michigan
- No categorizado Wiha
- No categorizado Beringer
- No categorizado Waterdrop
- No categorizado Revamp
- No categorizado Phonic
- No categorizado Rothenberger
- No categorizado Creamsource
- No categorizado ZCover
- No categorizado Vasagle
- No categorizado Lewitt
- No categorizado Aquatica
- No categorizado Girmi
- No categorizado Goaliath
- No categorizado 909 Outdoor
- No categorizado Viomi
- No categorizado Grimm Audio
- No categorizado Kahayan
- No categorizado Better Life
- No categorizado Dayclocks
- No categorizado Phidgets
- No categorizado TK Audio
- No categorizado Postium
- No categorizado Hawk-Woods
- No categorizado Novo
- No categorizado Commercial Chef
- No categorizado Novis
- No categorizado IsoAcoustics
- No categorizado Memphis
- No categorizado Alpha Tools
- No categorizado Engel
- No categorizado Clifford
- No categorizado Atlona
- No categorizado AVMATRIX
- No categorizado Cambo
- No categorizado Hedbox
- No categorizado Campart
- No categorizado Lansinoh
- No categorizado Adviti
- No categorizado Maclean
- No categorizado 9.solutions
- No categorizado Grundfos
- No categorizado Hotone
- No categorizado WEN
- No categorizado Lockwood
- No categorizado Kospel
- No categorizado Nexera
- No categorizado Goodway
- No categorizado BlueDri
- No categorizado Seenergy
- No categorizado Meinl
- No categorizado Analogis
- No categorizado BBQ Premium
- No categorizado Stäubli
- No categorizado RAB
- No categorizado Schabus
- No categorizado Eoslift
- No categorizado Bron-Coucke
- No categorizado Steelton
- No categorizado FeinTech
- No categorizado BioChef
- No categorizado Masterbuilt
- No categorizado T-Rex
- No categorizado Waterco
- No categorizado Kindercraft
- No categorizado Euro Cuisine
- No categorizado GFM
- No categorizado Tot Tutors
- No categorizado X4 Life
- No categorizado Ugreen
- No categorizado Tonar
- No categorizado Peterson
- No categorizado CFH
- No categorizado BOB Gear
- No categorizado Emeril Everyday
- No categorizado Könner & Söhnen
- No categorizado Rockboard
- No categorizado Goodis
- No categorizado Nivian
- No categorizado L.R.Baggs
- No categorizado Millennia
- No categorizado Vermona Modular
- No categorizado Adventure Kings
- No categorizado Drive Medical
- No categorizado Hitron
- No categorizado Bliss Hammocks
- No categorizado Singular Sound
- No categorizado Maneco Labs
- No categorizado BISWIND
- No categorizado ABE Arnhold
- No categorizado Mermade Hair
- No categorizado Hover-1
- No categorizado VCM
- No categorizado BodyCraft
- No categorizado Auer Signal
- No categorizado BrightSign
- No categorizado Mamas & Papas
- No categorizado Manduca
- No categorizado HELGI
- No categorizado Forge Adour
- No categorizado Eliminator Lighting
- No categorizado Darkglass
- No categorizado Blow
- No categorizado Paasche
- No categorizado Vistus
- No categorizado GMW
- No categorizado AER
- No categorizado Dynavox
- No categorizado Columbus
- No categorizado IWH
- No categorizado Code Mercenaries
- No categorizado SoundMagic
- No categorizado Diamex
- No categorizado Sunset
- No categorizado Avital
- No categorizado Ondis24
- No categorizado D'Addario
- No categorizado BBE
- No categorizado Lemair
- No categorizado Warwick
- No categorizado MyAVR
- No categorizado EBS
- No categorizado WEICON
- No categorizado Rotronic
- No categorizado Edsyn
- No categorizado Urban Glide
- No categorizado EISL
- No categorizado RCS
- No categorizado ARC
- No categorizado Nicai Systems
- No categorizado IDENTsmart
- No categorizado Altrad
- No categorizado Revier Manager
- No categorizado Homak
- No categorizado Statron
- No categorizado Tycon Systems
- No categorizado Selve
- No categorizado Lumel
- No categorizado Paingone
- No categorizado Howard Leight
- No categorizado Plugwise
- No categorizado Martens
- No categorizado Palmako
- No categorizado Desview
- No categorizado ActiveJet
- No categorizado Global Water
- No categorizado Allsee
- No categorizado Softing
- No categorizado Pulse ShowerSpas
- No categorizado Alogic
- No categorizado GFB
- No categorizado Sonicsmith
- No categorizado Toraiz
- No categorizado Ergodyne
- No categorizado Maturmeat
- No categorizado D-Jix
- No categorizado Orbsmart
- No categorizado Eowave
- No categorizado Arkon
- No categorizado Imperia
- No categorizado Nature2
- No categorizado AMERRY
- No categorizado Walther
- No categorizado ShelterLogic
- No categorizado Varad
- No categorizado Dr. Browns
- No categorizado Woods
- No categorizado UDG Gear
- No categorizado KMA Machines
- No categorizado CEDAR
- No categorizado Klark Teknik
- No categorizado Elcom
- No categorizado Source Audio
- No categorizado AtomoSynth
- No categorizado Innr
- No categorizado Benidub
- No categorizado Protector
- No categorizado Winston
- No categorizado Solidsteel
- No categorizado Lectrosonics
- No categorizado Dracast
- No categorizado Dream
- No categorizado Malouf
- No categorizado Roba
- No categorizado Ravelli
- No categorizado Piet Boon
- No categorizado PureTools
- No categorizado JML
- No categorizado Reber
- No categorizado SiriusXM
- No categorizado Earthwise
- No categorizado DoubleSight
- No categorizado Raya
- No categorizado NANO Modules
- No categorizado Artex
- No categorizado Bobrick
- No categorizado Verbos Electronics
- No categorizado Ark
- No categorizado DLO
- No categorizado ENS
- No categorizado Listen
- No categorizado Pentair
- No categorizado Oscium
- No categorizado Benchmark USA
- No categorizado Python
- No categorizado Littelfuse
- No categorizado Game Factor
- No categorizado NComputing
- No categorizado Mode Machines
- No categorizado Legends
- No categorizado AS Synthesizers
- No categorizado Itechworld
- No categorizado Nexcom
- No categorizado Janitza
- No categorizado SatKing
- No categorizado Fulltone
- No categorizado Advantix
- No categorizado Wampler
- No categorizado Hosa
- No categorizado VAEMI
- No categorizado Aguilar
- No categorizado Narva
- No categorizado DOK
- No categorizado OzCharge
- No categorizado MIYO
- No categorizado Cioks
- No categorizado Neopower
- No categorizado AvMap
- No categorizado Arlec
- No categorizado Sanwa
- No categorizado REDARC
- No categorizado Guardian
- No categorizado Radio Flyer
- No categorizado Gaslock
- No categorizado Gaffgun
- No categorizado AquaMAX
- No categorizado DigitSole
- No categorizado Portsmith
- No categorizado Flame
- No categorizado Rome
- No categorizado DW
- No categorizado BEA
- No categorizado Disty
- No categorizado OXI Instruments
- No categorizado AvaTime
- No categorizado Xhose
- No categorizado MYVU
- No categorizado Kopykake
- No categorizado Konstant Lab
- No categorizado Turbo Scrub
- No categorizado Tenderfoot Electronics
- No categorizado Kask
- No categorizado Callpod
- No categorizado Dorman
- No categorizado 2box
- No categorizado Enlight
- No categorizado Franken
- No categorizado RUBI
- No categorizado Europa Leisure
- No categorizado GAMO
- No categorizado Musser
- No categorizado Edge Products
- No categorizado IClever
- No categorizado HN-Power
- No categorizado BIONIK
- No categorizado King Canopy
- No categorizado HeadRush
- No categorizado Flover
- No categorizado Milestone Systems
- No categorizado Micsig
- No categorizado Dodow
- No categorizado Spring
- No categorizado Red Panda
- No categorizado OJ ELECTRONICS
- No categorizado Aquasure
- No categorizado Banana Pi
- No categorizado Ilford
- No categorizado TensCare
- No categorizado American International
- No categorizado Crazy Tube Circuits
- No categorizado J.P. Instruments
- No categorizado GMB Gaming
- No categorizado Proclip
- No categorizado SainSmart
- No categorizado Kaona
- No categorizado Baja Mobility
- No categorizado DPW Design
- No categorizado SinuPulse
- No categorizado The T.bone
- No categorizado DIEZEL
- No categorizado VMB
- No categorizado Z.Vex
- No categorizado Seymour Duncan
- No categorizado BluGuitar
- No categorizado Lehle
- No categorizado Bricasti Design
- No categorizado T.akustik
- No categorizado Dwarf Connection
- No categorizado JL Cooper
- No categorizado StrikeMaster
- No categorizado ProUser
- No categorizado Bēm Wireless
- No categorizado Millecroquettes
- No categorizado GR Bass
- No categorizado WilTec
- No categorizado Sure-Fi
- No categorizado Copernicus
- No categorizado Gumdrop
- No categorizado Tellur
- No categorizado Woox
- No categorizado Gallien-Krueger
- No categorizado Jetway
- No categorizado Texsport
- No categorizado SSV Works
- No categorizado Terre
- No categorizado Sanitec
- No categorizado Pangea Audio
- No categorizado Hogue
- No categorizado ATP
- No categorizado Pfannenberg
- No categorizado Scytek
- No categorizado MotorScrubber
- No categorizado Lupine
- No categorizado Kraftmax
- No categorizado Steelplay
- No categorizado PCTV Systems
- No categorizado Cooper Lighting
- No categorizado Sound Devices
- No categorizado Code Corporation
- No categorizado Now TV
- No categorizado Beautiful
- No categorizado Best Fitness
- No categorizado Voodoo Lab
- No categorizado Strymon
- No categorizado Insect Lore
- No categorizado Faytech
- No categorizado Chrome-Q
- No categorizado Kitronik
- No categorizado Trasman
- No categorizado Hamlet
- No categorizado SumUp
- No categorizado Microlab
- No categorizado Rotolight
- No categorizado Mr Gardener
- No categorizado Paladin
- No categorizado Lumu
- No categorizado Salicru
- No categorizado WAYDOO
- No categorizado Fimer
- No categorizado ASIWO
- No categorizado Vankyo
- No categorizado OWC
- No categorizado Lexar
- No categorizado Equip
- No categorizado Vivolink
- No categorizado Vent-Axia
- No categorizado Firefield
- No categorizado E-Power
- No categorizado RectorSeal
- No categorizado Red Digital Cinema
- No categorizado Beautifly
- No categorizado Kaiser Nienhaus
- No categorizado Freeplay
- No categorizado Roller Grill
- No categorizado DCS
- No categorizado Zaor
- No categorizado Glorious
- No categorizado Sensei
- No categorizado Cleco
- No categorizado AVTech
- No categorizado Dataflex
- No categorizado Bugera
- No categorizado Handy Lux
- No categorizado Rossum Electro-Music
- No categorizado Panta
- No categorizado Pentel
- No categorizado Gima
- No categorizado MagnaPool
- No categorizado Aquadon
- No categorizado Raidsonic
- No categorizado Approx
- No categorizado Gamesir
- No categorizado Neunaber
- No categorizado Leotec
- No categorizado VOREL
- No categorizado Ciarra
- No categorizado Ocean Way Audio
- No categorizado DayStar Filters
- No categorizado Flexispot
- No categorizado OP/TECH
- No categorizado Alfatron
- No categorizado ETC
- No categorizado Vertex
- No categorizado Nuki
- No categorizado SWIT
- No categorizado EOTech
- No categorizado Cinderella
- No categorizado Bauhn
- No categorizado Aspen
- No categorizado Cottons
- No categorizado Key Digital
- No categorizado TVLogic
- No categorizado CAD Audio
- No categorizado Frequency Central
- No categorizado Sacrament
- No categorizado The Box
- No categorizado AudioThing
- No categorizado Feelworld
- No categorizado Cambium Networks
- No categorizado Trident
- No categorizado Schoeps
- No categorizado HPI Racing
- No categorizado Trijicon
- No categorizado Favini
- No categorizado Dnipro
- No categorizado Dot Line
- No categorizado Polsen
- No categorizado KJB Security Products
- No categorizado IFootage
- No categorizado Sonuus
- No categorizado Whirlwind
- No categorizado Cabasse
- No categorizado Jonsered
- No categorizado Saint Algue
- No categorizado Cactus
- No categorizado Musical Fidelity
- No categorizado Oecolux
- No categorizado Core SWX
- No categorizado Multibrackets
- No categorizado SoundLAB
- No categorizado ACL
- No categorizado SurgeX
- No categorizado Mars Gaming
- No categorizado Radiant
- No categorizado Roadinger
- No categorizado G.Skill
- No categorizado Edbak
- No categorizado Integral LED
- No categorizado Integral
- No categorizado Virax
- No categorizado MSW
- No categorizado Amaran
- No categorizado Gill
- No categorizado AMC
- No categorizado Triangle
- No categorizado Rittal
- No categorizado I-Tec
- No categorizado Majestic
- No categorizado Anthro
- No categorizado Tumbleweed
- No categorizado Alutruss
- No categorizado Sunpentown
- No categorizado Hamstra
- No categorizado PVI
- No categorizado OKAY
- No categorizado Avenview
- No categorizado Grendel
- No categorizado Coravin
- No categorizado Phoenix Gold
- No categorizado Weidmüller
- No categorizado BSS Audio
- No categorizado O&O Software
- No categorizado Wasp
- No categorizado Chef's Choice
- No categorizado Ciclo
- No categorizado Warmup
- No categorizado Brastemp
- No categorizado Wavtech
- No categorizado Satco
- No categorizado AMT
- No categorizado Royal Catering
- No categorizado Artrom
- No categorizado Lowell
- No categorizado Adonit
- No categorizado Point Source Audio
- No categorizado ANDYCINE
- No categorizado AmpliVox
- No categorizado SEIKI
- No categorizado Pippi
- No categorizado Memphis Audio
- No categorizado Casalux
- No categorizado CyberData Systems
- No categorizado Omnitron Systems
- No categorizado Stewart Systems
- No categorizado SwitchBot
- No categorizado AMX
- No categorizado Qubino
- No categorizado Eurosound
- No categorizado BZBGear
- No categorizado Rolls
- No categorizado WyreStorm
- No categorizado K&M
- No categorizado Magewell
- No categorizado Rocstor
- No categorizado Globalo
- No categorizado Adam Hall
- No categorizado Flaem
- No categorizado Therabody
- No categorizado Infortrend
- No categorizado STI
- No categorizado Rug Doctor
- No categorizado Raspberry Pi
- No categorizado Bals
- No categorizado Balt
- No categorizado FIAP
- No categorizado Perixx
- No categorizado AJ.BA
- No categorizado ESKA
- No categorizado Lascar Electronics
- No categorizado EWON
- No categorizado Sport-Tronic
- No categorizado Alga
- No categorizado WesAudio
- No categorizado Hamron
- No categorizado Robust
- No categorizado Heritage Audio
- No categorizado Quik Lok
- No categorizado Tsakalis AudioWorks
- No categorizado MagTek
- No categorizado QOMO
- No categorizado MAK
- No categorizado Drake
- No categorizado Jupiter
- No categorizado Sony Optiarc
- No categorizado Colortone
- No categorizado Anybus
- No categorizado Super Rod
- No categorizado Carnielli
- No categorizado Luminex
- No categorizado Epiphan
- No categorizado XS Power
- No categorizado Babybjörn
- No categorizado Deltaco Gaming
- No categorizado P3 International
- No categorizado Idec
- No categorizado Beckmann & Egle
- No categorizado Seek Thermal
- No categorizado VintageView
- No categorizado Alfresco
- No categorizado Bintec-elmeg
- No categorizado Crane Song
- No categorizado W'eau
- No categorizado Ixxat
- No categorizado Belena
- No categorizado Fanox
- No categorizado Crouzet
- No categorizado Megarevo
- No categorizado Tech 21
- No categorizado Petmate
- No categorizado BlendMount
- No categorizado Perlick
- No categorizado Sedona
- No categorizado Tecnoinox
- No categorizado CaterRacks
- No categorizado Besco
- No categorizado Prologue
- No categorizado Scotsman
- No categorizado Atosa
- No categorizado Nanoleaf
- No categorizado Mach Power
- No categorizado Soltection
- No categorizado Kool-It
- No categorizado Cool Head
- No categorizado KeepOut
- No categorizado LawnMaster
- No categorizado Deltronic
- No categorizado Eligent
- No categorizado Meris
- No categorizado Procare
- No categorizado AmerBox
- No categorizado Qu-Bit
- No categorizado Blue Lantern
- No categorizado CTA Digital
- No categorizado DivKid
- No categorizado Panamax
- No categorizado MBM
- No categorizado FaseLunare
- No categorizado Götze & Jensen
- No categorizado Twinkly
- No categorizado Squarp Instruments
- No categorizado EtherWAN
- No categorizado Econ Connect
- No categorizado META
- No categorizado GC Audio
- No categorizado Einhell Bavaria
- No categorizado Motrona
- No categorizado Thalheimer
- No categorizado Ergotools Pattfield
- No categorizado Proviel
- No categorizado FeiYu-Tech
- No categorizado Aida
- No categorizado Apantac
- No categorizado VisionTek
- No categorizado MuxLab
- No categorizado Accsoon
- No categorizado FeiyuTech
- No categorizado Losi
- No categorizado Bessey
- No categorizado A3
- No categorizado Serge
- No categorizado Gladiator
- No categorizado Mobli
- No categorizado Sonoff
- No categorizado G-Technology
- No categorizado Caroma
- No categorizado Sungale
- No categorizado Befaco
- No categorizado Waltec
- No categorizado Elvid
- No categorizado Portkeys
- No categorizado Westcott
- No categorizado Sky-Watcher
- No categorizado Tempo
- No categorizado EXSYS
- No categorizado Digiquest
- No categorizado Gewiss
- No categorizado Hagor
- No categorizado Glyph
- No categorizado Seco-Larm
- No categorizado Camille Bauer
- No categorizado Murr Elektronik
- No categorizado Massoth
- No categorizado Envitec
- No categorizado Mimo Monitors
- No categorizado Alula
- No categorizado Blebox
- No categorizado VS Sassoon
- No categorizado Bright Spark
- No categorizado Peloton
- No categorizado Gentrax
- No categorizado Gamber-Johnson
- No categorizado Brocade
- No categorizado ICC
- No categorizado Insteon
- No categorizado Amer
- No categorizado Altronix
- No categorizado Juniper
- No categorizado Warner Bros
- No categorizado Vinotemp
- No categorizado Silent Knight
- No categorizado Mosconi
- No categorizado Ditek
- No categorizado Kingston Technology
- No categorizado Axxess
- No categorizado Wilson
- No categorizado Goki
- No categorizado CGV
- No categorizado My Arcade
- No categorizado Enttec
- No categorizado Tescoma
- No categorizado RF Elements
- No categorizado ALC
- No categorizado Holland Electronics
- No categorizado Arista
- No categorizado Chenbro Micom
- No categorizado Brentwood
- No categorizado Triumph Sports
- No categorizado Gasmate
- No categorizado Crelando
- No categorizado Novo Nordisk
- No categorizado Seville Classics
- No categorizado DeepCool
- No categorizado TechLogix Networx
- No categorizado SunBriteTV
- No categorizado NuTone
- No categorizado Thermalright
- No categorizado Meross
- No categorizado EchoMaster
- No categorizado Bxterra
- No categorizado Bea-fon
- No categorizado Renogy
- No categorizado Babylonia
- No categorizado HeartSine
- No categorizado Bullet
- No categorizado Morrison
- No categorizado Ordo
- No categorizado Noctua
- No categorizado Alphacool
- No categorizado Asetek
- No categorizado Biostar
- No categorizado TechN
- No categorizado Eversolo
- No categorizado Davita
- No categorizado Giga Copper
- No categorizado Elsner
- No categorizado Séura
- No categorizado Cube Controls
- No categorizado Meridian
- No categorizado Donexon
- No categorizado Eve Audio
- No categorizado Axagon
- No categorizado Linq
- No categorizado Wortmann AG
- No categorizado AEA
- No categorizado DiGiGrid
- No categorizado Sanofi
- No categorizado Mitzu
- No categorizado Avteq
- No categorizado Seaward
- No categorizado Omega Altise
- No categorizado Fizzics
- No categorizado XFX
- No categorizado Leynew
- No categorizado Lauten Audio
- No categorizado Cropico
- No categorizado Sunwoda
- No categorizado Schleich
- No categorizado Unitech
- No categorizado FXLab
- No categorizado Middle Atlantic
- No categorizado Kincrome
- No categorizado Vincent
- No categorizado BC Acoustique
- No categorizado Brockhaus HEUER
- No categorizado National Geographic
- No categorizado Reishunger
- No categorizado Ergotec
- No categorizado Dupla
- No categorizado APSystems
- No categorizado IODD
- No categorizado BYD
- No categorizado Tektronix
- No categorizado Aqua Medic
- No categorizado Pylontech
- No categorizado Fire Sense
- No categorizado Grüniq
- No categorizado Goodwe
- No categorizado Moki
- No categorizado Enertex
- No categorizado IOTAVX
- No categorizado Ovation
- No categorizado InAlto
- No categorizado MDT
- No categorizado Enviroswim
- No categorizado Dobar
- No categorizado Vevor
- No categorizado Ovente
- No categorizado PowerColor
- No categorizado ISpring
- No categorizado WeFix
- No categorizado BCA
- No categorizado Serpent
- No categorizado Saki
- No categorizado Smart365
- No categorizado Fosi Audio
- No categorizado ChargeHub
- No categorizado Eldat
- No categorizado NEP
- No categorizado SoundSwitch
- No categorizado Sera
- No categorizado Dostmann Electronic
- No categorizado A-NeuVideo
- No categorizado Murideo
- No categorizado ToughTested
- No categorizado JBC
- No categorizado DV Mark
- No categorizado MOON
- No categorizado Cuggl
- No categorizado HABAU
- No categorizado CVW
- No categorizado Majority
- No categorizado Earbreeze
- No categorizado S.M.S.L
- No categorizado Möhlenhoff
- No categorizado Taqua
- No categorizado NightStick
- No categorizado ChyTV
- No categorizado Brainstorm
- No categorizado Colonial Elegance
- No categorizado Overtone Labs
- No categorizado IBEAM
- No categorizado Bühnen
- No categorizado Blukac
- No categorizado BendixKing
- No categorizado Tube-Tech
- No categorizado TCW Technologies
- No categorizado UNITEK
- No categorizado CoolerMaster
- No categorizado NuPrime
- No categorizado The T.mix
- No categorizado Regula-Werk King
- No categorizado Inter-M
- No categorizado MIDI Solutions
- No categorizado Positive Grid
- No categorizado Amgrow
- No categorizado Xaphoon
- No categorizado Winchester
- No categorizado Lampa
- No categorizado Sinus Live
- No categorizado Sureguard
- No categorizado QuickCool
- No categorizado Smit Visual
- No categorizado NZR
- No categorizado Toparc
- No categorizado Oro-Med
- No categorizado Hex
- No categorizado Baby Cakes
- No categorizado Deflecto
- No categorizado ELMEKO
- No categorizado Tesseract Modular
- No categorizado Sport Dog
- No categorizado Nowsonic
- No categorizado On Air
- No categorizado Acoustic Solutions
- No categorizado E-ast
- No categorizado Hubble Connected
- No categorizado ELTA Music
- No categorizado Oliveri
- No categorizado Dragonshock
- No categorizado We-Vibe
- No categorizado Electronics International
- No categorizado Lamar
- No categorizado Atlantis Land
- No categorizado White Lightning
- No categorizado Deye
- No categorizado My Wall
- No categorizado GEV
- No categorizado Frient
- No categorizado Kaiser Fototechnik
- No categorizado Hoymiles
- No categorizado Vishay
- No categorizado Rooboost
- No categorizado Bitspower
- No categorizado JMAZ Lighting
- No categorizado EAT
- No categorizado Comar
- No categorizado Freedor
- No categorizado Start International
- No categorizado C2G
- No categorizado AXITEC
- No categorizado Lingg & Janke
- No categorizado Auralex
- No categorizado Pieps
- No categorizado Innovative
- No categorizado Lynx Technik
- No categorizado Yuede
- No categorizado ClimeMET
- No categorizado Pliant Technologies
- No categorizado Prompter People
- No categorizado Astropet
- No categorizado Busch + Müller
- No categorizado Canopia
- No categorizado Wabeco
- No categorizado Swingline GBC
- No categorizado Spelsberg
- No categorizado Staudte-Hirsch
- No categorizado Universal Remote Control
- No categorizado Soundsphere
- No categorizado Lantronix
- No categorizado Kino Flo
- No categorizado Aqua Computer
- No categorizado HEDD
- No categorizado Vinpower Digital
- No categorizado Lindemann
- No categorizado Silent Angel
- No categorizado Bavaria By Einhell
- No categorizado Healthy Choice
- No categorizado IOptron
- No categorizado Bbf
- No categorizado Club 3D
- No categorizado Sprolink
- No categorizado Thermionic Culture
- No categorizado Watercool
- No categorizado Moultrie
- No categorizado Skaarhoj
- No categorizado Microboards
- No categorizado Whitestone
- No categorizado BMB
- No categorizado Advance
- No categorizado Arylic
- No categorizado Gem Toys
- No categorizado Mount-It!
- No categorizado Cloud
- No categorizado Sandia Aerospace
- No categorizado EK Water Blocks
- No categorizado Lamptron
- No categorizado PS Audio
- No categorizado Gudsen
- No categorizado Zendure
- No categorizado Envertech
- No categorizado Phanteks
- No categorizado Prism Sound
- No categorizado MoFi
- No categorizado Gosund
- No categorizado ID-Tech
- No categorizado Artecta
- No categorizado DMT
- No categorizado FSP/Fortron
- No categorizado IDIS
- No categorizado CM Storm
- No categorizado MARTOR
- No categorizado SMART Technologies
- No categorizado Lumantek
- No categorizado Audiotec Fischer
- No categorizado SEADA
- No categorizado Honey-Can-Do
- No categorizado Promise Technology
- No categorizado Deity
- No categorizado Patriot
- No categorizado B.E.G.
- No categorizado Fixpoint
- No categorizado Enerdrive
- No categorizado Respironics
- No categorizado ChamSys
- No categorizado TESLA Electronics
- No categorizado Intesis
- No categorizado Nethix
- No categorizado Pluto
- No categorizado Laine
- No categorizado 3Doodler
- No categorizado Soundskins
- No categorizado Middle Atlantic Products
- No categorizado Doepke
- No categorizado Datapath
- No categorizado Loctite
- No categorizado Antelope
- No categorizado Vertiv
- No categorizado Astera
- No categorizado Polyend
- No categorizado Sabco
- No categorizado Sensative
- No categorizado Plasma Cloud
- No categorizado Flo
- No categorizado Sheeran Looper
- No categorizado Applico
- No categorizado Jungle Gym
- No categorizado Smart Media
- No categorizado TOGU
- No categorizado BLUEPALM
- No categorizado Hacienda
- No categorizado Christmaxx
- No categorizado IStarUSA
- No categorizado Code
- No categorizado Mivar
- No categorizado SolaX Power
- No categorizado IPGARD
- No categorizado Weston
- No categorizado EZ Dupe
- No categorizado AURALiC
- No categorizado Absco
- No categorizado Schatten Design
- No categorizado LEDs-ON
- No categorizado Bestgreen
- No categorizado MyPOS
- No categorizado Truetone
- No categorizado Stages
- No categorizado Starlink
- No categorizado HDFury
- No categorizado Favero
- No categorizado Durvet
- No categorizado KNEKT
- No categorizado Gator Frameworks
- No categorizado Teia
- No categorizado The Joy Factory
- No categorizado Yuer
- No categorizado OLLO
- No categorizado Axor
- No categorizado Gustard
- No categorizado Enhance
- No categorizado MEPROLIGHT
- No categorizado Tactical Fiber Systems
- No categorizado GVision
- No categorizado Veber
- No categorizado PurAthletics
- No categorizado SMS
- No categorizado Carlo Gavazzi
- No categorizado Richgro
- No categorizado Varaluz
- No categorizado Milesight
- No categorizado Dehner
- No categorizado Edwards
- No categorizado Victor Technology
- No categorizado Lastolite
- No categorizado Lowepro
- No categorizado MIOPS
- No categorizado Bluebird
- No categorizado Cotek
- No categorizado EA Elektro Automatik
- No categorizado CMI
- No categorizado Grand Effects
- No categorizado SunPower
- No categorizado Hensel
- No categorizado Westland
- No categorizado Bahr
- No categorizado Black Line
- No categorizado Sodapop
- No categorizado Enbrighten
- No categorizado Vicoustic
- No categorizado Albert Heijn
- No categorizado Yphix
- No categorizado TAURUS Titanium
- No categorizado Magliner
- No categorizado Magmatic
- No categorizado Comfortisse
- No categorizado Cayin
- No categorizado Ambient Weather
- No categorizado Videotel Digital
- No categorizado Zylight
- No categorizado Smith-Victor
- No categorizado HuddleCamHD
- No categorizado Technical Pro
- No categorizado MooreCo
- No categorizado BIOS Living
- No categorizado Connection
- No categorizado Blind Spot
- No categorizado Badiona
- No categorizado VMV
- No categorizado Digigram
- No categorizado Mutec
- No categorizado Beghelli
- No categorizado Black Hydra
- No categorizado Expressive E
- No categorizado Merging
- No categorizado Bellari
- No categorizado CSL
- No categorizado Altman
- No categorizado Hawke
- No categorizado Defender
- No categorizado Betty Bossi
- No categorizado FoxFury
- No categorizado Eller
- No categorizado Rotatrim
- No categorizado Peak Design
- No categorizado Uniropa
- No categorizado ESE
- No categorizado Claypaky
- No categorizado Casa Deco
- No categorizado Hecate
- No categorizado Jinbei
- No categorizado Christmas Time
- No categorizado Comprehensive
- No categorizado Dobot
- No categorizado Nearity
- No categorizado Easyrig
- No categorizado Digitalinx
- No categorizado Gra-Vue
- No categorizado WHD
- No categorizado Sumiko
- No categorizado TechBite
- No categorizado Blackburn
- No categorizado Inverx
- No categorizado Primewire
- No categorizado XCell
- No categorizado Yellow Garden Line
- No categorizado Titanwolf
- No categorizado Uplink
- No categorizado Mybeo
- No categorizado Medicinalis
- No categorizado Bearware
- No categorizado Liam&Daan
- No categorizado Traco Power
- No categorizado Microair
- No categorizado Perfect Christmas
- No categorizado Bebob
- No categorizado Fiilex
- No categorizado PTZ Optics
- No categorizado Xcellon
- No categorizado Sescom
- No categorizado Robus
- No categorizado CAME-TV
- No categorizado Rosco
- No categorizado Wimberley
- No categorizado Nureva
- No categorizado Revic
- No categorizado Galcon
- No categorizado Telmax
- No categorizado Apollo Design
- No categorizado DEERSYNC
- No categorizado Gen Energy
- No categorizado JoeCo
- No categorizado Holosun
- No categorizado Aconatic
- No categorizado Kluge
- No categorizado Arovec
- No categorizado SecureSafe
- No categorizado CubuSynth
- No categorizado Exelpet
- No categorizado Aplic
- No categorizado Imarflex
- No categorizado Analog Way
- No categorizado Tempmate
- No categorizado Stalco
- No categorizado Carlsbro
- No categorizado Ventev
- No categorizado Mobotix
- No categorizado Steelbody
- No categorizado PureLink
- No categorizado UNYKAch
- No categorizado VAVA
- No categorizado Mammut
- No categorizado Modbap Modular
- No categorizado Bluestork
- No categorizado INOGENI
- No categorizado Carry-on
- No categorizado AddLiving
- No categorizado IOIO
- No categorizado Nimbus
- No categorizado City Theatrical
- No categorizado Acros
- No categorizado Redback Technologies
- No categorizado Vent-A-Hood
- No categorizado GoXtreme
- No categorizado Bome
- No categorizado One Control
- No categorizado EQ Acoustics
- No categorizado AV Tool
- No categorizado Aquael
- No categorizado NEXTO DI
- No categorizado Thermarest
- No categorizado Fortinge
- No categorizado RF-Links
- No categorizado LiveU
- No categorizado Austral
- No categorizado Cherub
- No categorizado ProLights
- No categorizado Xinfrared
- No categorizado Brizo
- No categorizado Europalms
- No categorizado DuroStar
- No categorizado Waterstone
- No categorizado Huslog
- No categorizado Mr Steam
- No categorizado DVDO
- No categorizado A-Designs
- No categorizado Henry Engineering
- No categorizado Primacoustic
- No categorizado HomeCraft
- No categorizado Heusinkveld
- No categorizado EnOcean
- No categorizado Storcube
- No categorizado Varia
- No categorizado Gurari
- No categorizado Fezz
- No categorizado ASI
- No categorizado Lexivon
- No categorizado Swiss Eye
- No categorizado Cane Creek
- No categorizado EPEVER
- No categorizado KED
- No categorizado Caberg
- No categorizado Exped
- No categorizado Edouard Rousseau
- No categorizado GameDay
- No categorizado Sparkle
- No categorizado Söll
- No categorizado X-Lite
- No categorizado AXESS
- No categorizado Glemm
- No categorizado Ridem
- No categorizado StarIink
- No categorizado Røde
- No categorizado Noyafa
- No categorizado Envertec
- No categorizado Nordic Winter
- No categorizado Volcano
- No categorizado Wire Technologies
- No categorizado Taco Tuesday
- No categorizado IMM Photonics
- No categorizado Field Optics
- No categorizado Robern
- No categorizado Signature Hardware
- No categorizado GRAUGEAR
- No categorizado Sure Petcare
- No categorizado Sortimo
- No categorizado Livall
- No categorizado Beaphar
- No categorizado Catit
- No categorizado Mebby
- No categorizado TONI&GUY
- No categorizado Balam Rush
- No categorizado Roesle
- No categorizado Oreg
- No categorizado Karran
- No categorizado OOONO
- No categorizado CaviLock
- No categorizado Origin Storage
- No categorizado Kostal
- No categorizado Ulsonix
- No categorizado Stamony
- No categorizado Pitsos
- No categorizado Yamazen
- No categorizado Lantus
Últimos No categorizado Manuales

27 Octubre 2024

Workzone 20V Li-Ion Reciprocating Saw PT160501 Manual de Usario
27 Octubre 2024
27 Octubre 2024

27 Octubre 2024

27 Octubre 2024

27 Octubre 2024

27 Octubre 2024

27 Octubre 2024

27 Octubre 2024

27 Octubre 2024